Casting company Sarginsons Industries has unveiled designs for an automotive subframe that was originally optimized for weight in 2022 and has now been reduced from 28kg to 15kg. The designs were formulated using new AI-driven software that is currently under development, and are the initial results of the Performance Integrated Vehicle Optimisation Technology (PIVOT) project, which Sarginsons is leading in collaboration with its partners. The project was made possible by a £6m (US$7.5m) matched grant from the Advanced Propulsion Centre and Innovate UK.
The software highlights where excess aluminum has been removed, showcasing the ability of the technology to simulate the part’s varying mechanical properties and place the right material in the right areas. Crucially, the achievement clearly demonstrates that automotive aluminum parts can be lighter without compromising their mechanical integrity.
Gavin Shipley, technical director at Sarginsons, said, “The designs don’t just look extraordinary, but by being 50% lighter, they are extraordinary. We have managed to overcome the complexities of simulating the yield, tensile strength and elongation of cast components. We can now predict, on a point-by-point basis across the entire form of the casting, its mechanical performance. This allows for true vehicle crash performance to be simulated for the first time. The ability to simulate and optimize casting performance at such a granular level means we can now produce organic, highly optimized designs that were previously beyond human imagination.
Sarginsons aims to produce the first physical casting using this technology by the summer.
Shipley continued, “The castings are also designed using secondary, fully recycled aluminum for the first time, meaning that the PIVOT research could also represent the single biggest step forward in vehicular carbon reduction since the advent of the electric car – while dramatically reducing the need for environmentally damaging extractive mining. The combined effect of all this technology is that we can finally fully exploit the full potential of liquid metal engineering to create almost any shape or size of component, with no loss of performance. That is a really exciting prospect, as we are paving the way for cars, planes, trains and drones to utilize this technology in the future to make them lighter, greener and more cost-effective.”
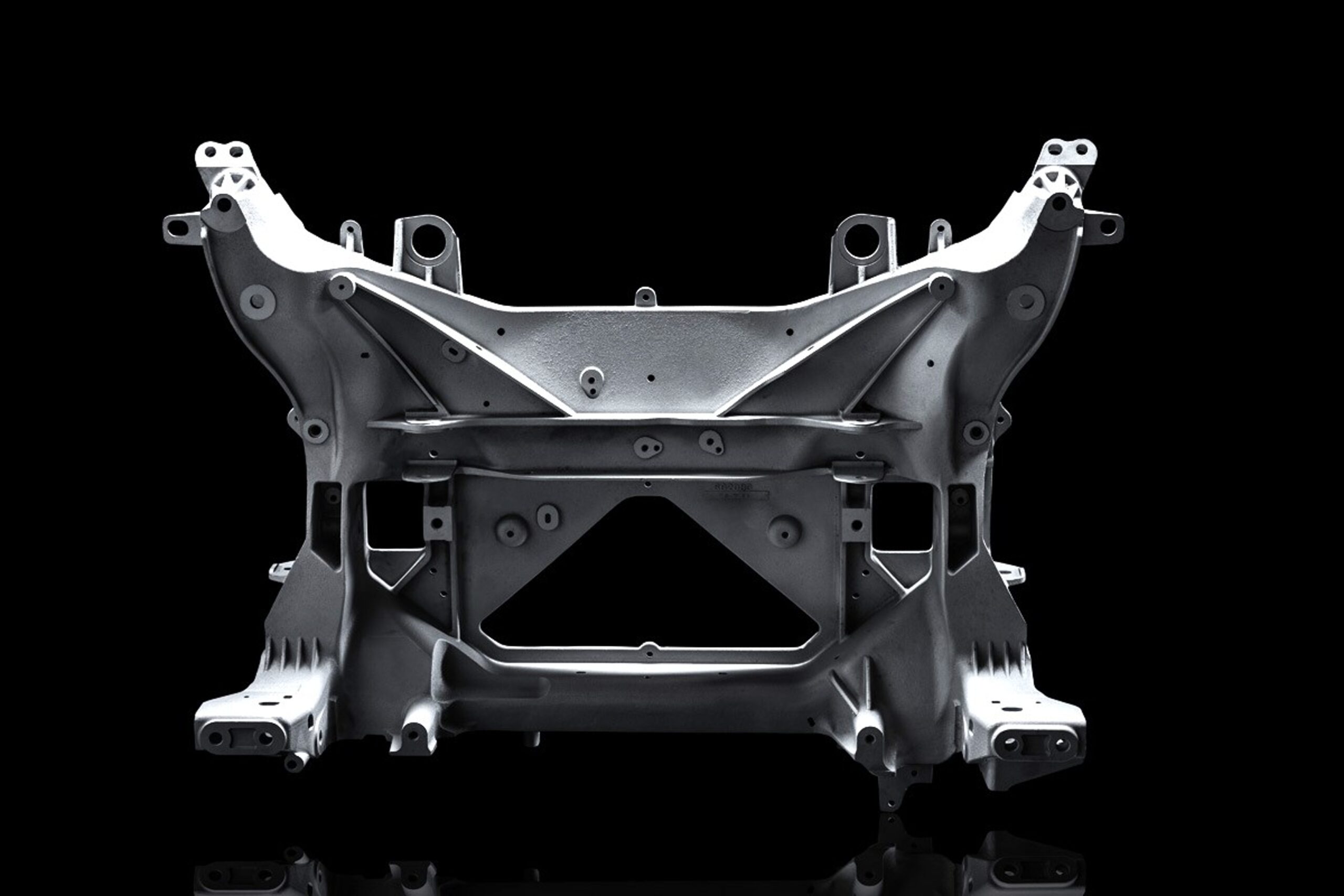