Virtual engineering continues to redefine the trajectory of automotive development, extending its transformative influence even to the realm of adhesive technologies
We are experiencing the most rapid period of change that automotive manufacturing has seen in the past several decades. The pressure to innovate quickly and efficiently has never been greater for both OEMs and suppliers. For adhesive companies focused on creating groundbreaking products, the ability to test, tweak and perfect ideas before a real-world part is made is invaluable. By harnessing the power of modeling and simulation, engineers at Sunstar Engineering are reimagining how the company’s products are developed, saving time, reducing cost and innovating better solutions to the needs of the market.
With computer-aided design and finite elemental analysis tools such as SolidWorks, Abaqus, Ansys and others, our scientists and engineers can use modeling and simulation to visualize designs, predict product behavior, optimize features early in the development cycle or troubleshoot issues occurring in real world application. These tools enable us to create digital versions of a product and trial it in a virtual environment, acting as a blueprint, prototype and testing ground – all within the bounds of a computer screen.
By experimenting in a virtual environment, we can test a product’s performance, durability and functionality in ways that were once only possible with real-world prototypes, which are often time intensive and costly to produce. By minimizing our reliance on physical modes, CAD and FEA tools enable us to allocate resources more efficiently and focus on high-impact changes that drive product success. Not only does this accelerate the design process, but it also brings about higher levels of creativity and innovation from our researchers.
According to Argonne National Laboratory, up to 90% of the emissions of a typical automotive factory come from the energy consumption and materials involved in the weld-shop and paint-shop processes. To meet ambitious governmental or industry-imposed carbon-neutral targets, OEMs have begun implementing changes to the way vehicles are being designed and made. On the design front, emphasis on lightweighting has seen the incorporation of more aluminum parts. On the manufacturing end, implementation of lower energy processes has led to the removal of ovens and reduction in oven temperatures used in weld and paint shops to cure adhesive, sealants and coatings. Combined, these changes challenge adhesive suppliers as the longstanding industry standard is a one-component application to steel with curing at relatively high temperature.
One example that illustrates the impact of modeling and simulation in action at Sunstar Engineering was during the development of a two-component anti-flutter adhesive designed for compact or low temperature curing weld-shop processes. Some OEMs have removed ovens used to build partial mechanical strength in adhesives applied to vehicles before they begin the electrocoating (e-coat) process, which can cause the adhesives to wash out of the joints they are meant to bond. To overcome this issue, an adhesive that can gel before the e-coat process without thermal input can be used. The challenge is making sure that the adhesive can maintain adhesion to the joint not only as it goes through the e-coat baths, but also during the e-coat oven.
For mixed material substrates, such as aluminum and steel systems, the differences in coefficients of thermal expansion can cause larger gaps between joints to form while heating than traditional all steel parts. With the proper inputs, this phenomenon can be modeled easily and used for the development of a solution to a given situation. In our case, a generic sedan hood with an inner and outer skin of 6016 4T aluminum was designed in SolidWorks. The modeled part was then tested in a simulated e-coat oven conditions (195°C x 15-minute keep time at 50W/(m²K)) using SolidWorks simulation.
The minimum and maximum joint expansion between the inner and outer skins of the hood was measured by the software after the simulation (Figure 1), and it was determined that an adhesive for this part and process would need to be able to span a gap of 16.9mm that formed during the e-coat oven process. To make an adhesive that could survive such a process, a customized real-world test method was made using a TA Discovery HR-1 Rheometer that enabled us to trial our adhesive under heated conditions at a rate that mimicked the rate of expansion simulated in SolidWorks. The result was an adhesive that can span a gap greater than 17mm (Figure 2). This case study not only helped us design a better adhesive, but the model enabled us to facilitate better conversations with our customers to help them understand the nuances of their own processes.
This is just one example of how Sunstar Engineering has used modeling and simulation to develop new products. As technology and the industry continues to evolve, so too does our modeling and simulation capability. AI-driven simulations using machine learning tools for design of experiments is enabling the company to analyze and interpret data, formulate and innovate with fewer experiments in the lab and helping us predict product performance with greater accuracy and more cost-effectiveness. These cutting-edge tools help our scientists and engineers visualize application needs in a more interactive and informed design process, not only improving our products but also transforming how we bring ideas to life.
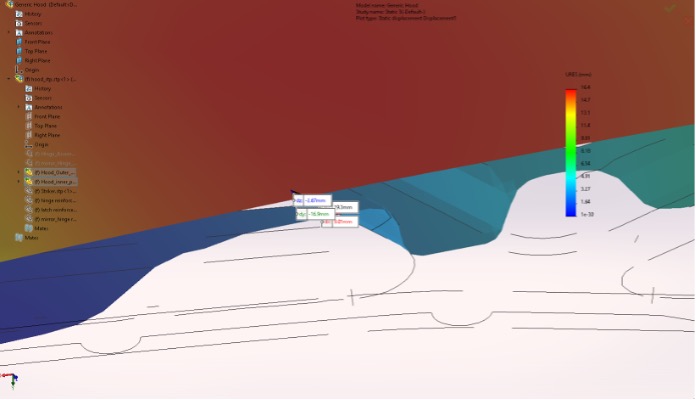
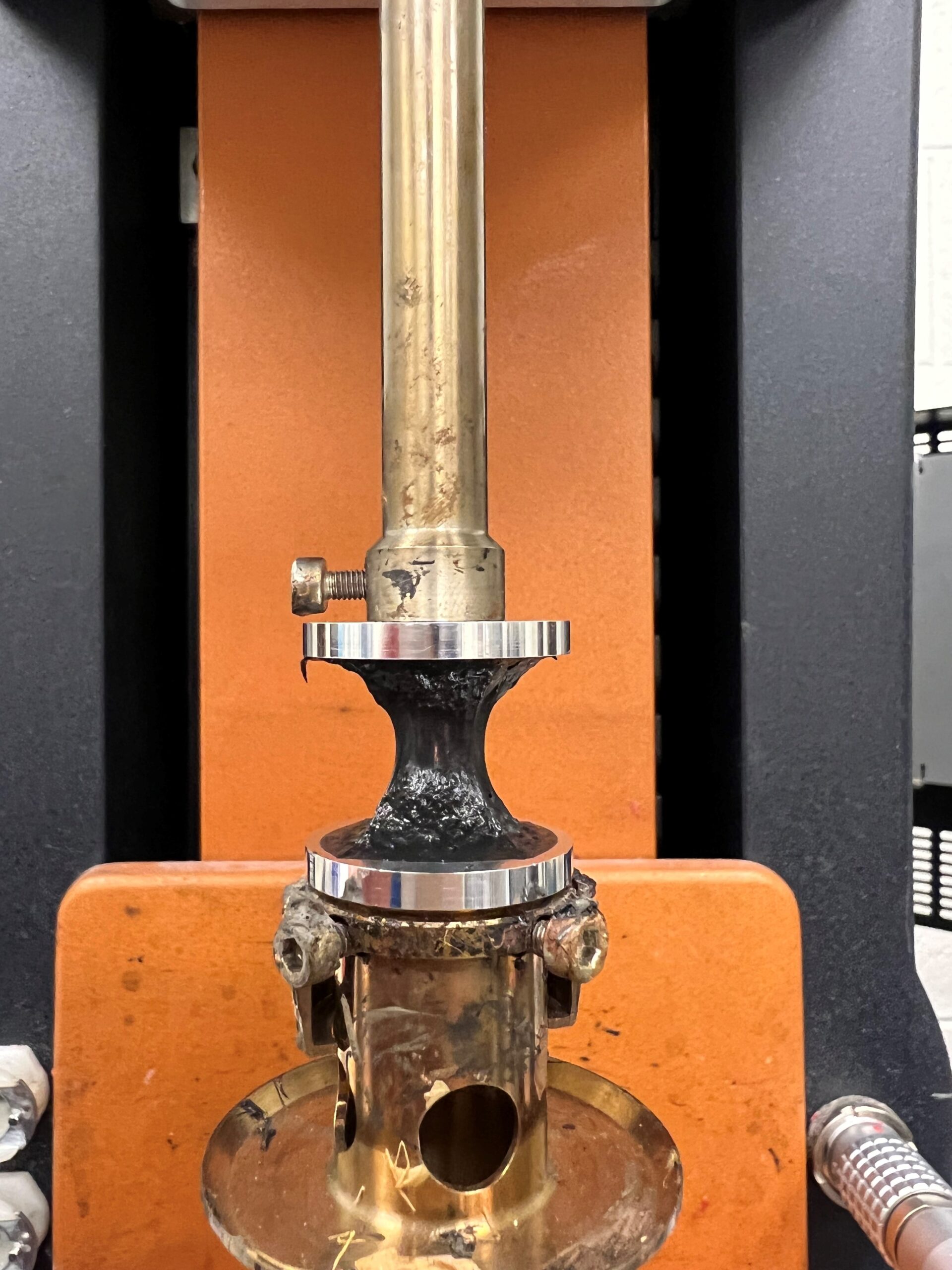
Nicholas Huff is manager, New Technology group, at Sunstar Engineering Americas. He holds an MSc in chemistry from the University of Florida and has worked at Sunstar since 2014. During his time in SEE’s R&D department, he has worked on a multitude of projects related to the development of sealants and adhesives for the automotive industry. As leader of the New Technology group, his team is responsible for the identification and implementation of long-term strategic research in areas of change and growth for Sunstar Engineering’s key industries, such as the shift to electric mobility, carbon neutrality, low-energy or compact process manufacturing, light-weighting, nanomaterials, AI/ML transformation and many others.