With vehicle development lead times now shorter than ever before, car manufacturers are relying on human-in-the-loop driving simulators to meet deadlines while also ensuring the validation of a growing number of driver assistance technologies. Phil Morse, technical liaison at Ansible Motion, offers insight into what we can expect from simulation in 2018.
With their ever-increasing presence, driving simulators appear to be the latest tool that vehicle constructors rely upon, but they have actually played a part in vehicle development for a long time. Take a look at Mercedes’ enormous simulator with an S-Class perched on top. In fact, simulators using Stewart Platforms (a.k.a. hexapods) were trialed for tire development in the late 1940s.
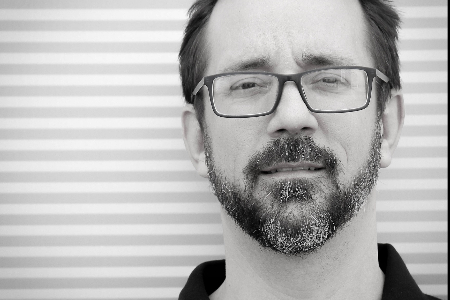
Developments in responsiveness, graphics, together with improvements in vehicle and road surface modeling fidelity, mean that today’s simulators offer the potential to do much more than 1940s technology. As we head to 2018, we have made the following predictions for simulation:
1. Looking back to look forward
With simulator technology now well-established, the big cues such as motion and graphics are well understood. Expect more focus on the smaller cues that deliver more realism via important subtleties. Rear-view emulation via wing and center mirrors is one example of graphics cueing that we predict will be popular in 2018. It’s this sense of realism that is exciting both road and race engineers and drivers looking for the most immersive experience. In the realm of motion cueing, look for supplemental systems that target specific sensory areas other than the human vestibular system, e.g. haptic devices aimed at delivering realism to driver/occupant touchpoints.
2. Applying pressure for braking technology
Tier 1 suppliers, safety groups and campaigners are going to be pushing even harder in 2018 for technologies such as AEB to become standard on cars. Using bespoke real-time software/hardware test benches such as dSpace enables systems to be verified on a sim by a wide range of drivers in a safe and controlled lab environment. For example, if an AEB engineer is limited to only a few weeks with a prototype vehicle to sort out a complete AEB deployment, time spent in a simulator lab means that time spent with the prototype car can be allocated to the pursuit of excellence rather than mere acceptance.
3. Getting to grips with complexity
Integrating real hardware into a simulation program is set to grow in 2018. It provides more representative results for on-car features such as traction control and V2X (vehicle-to-anything). In many cases, prototype hardware (sensor and logic arrays, etc) exist in advance of the vehicles into which they might be deployed. In such cases, software and hardware simulation fusion is required, wherein test benches must be connected to driving simulators in order to assess function and/or performance.
4. Electro-magnetism
EVs will be necessary for most V2I (vehicle-to-infrastructure) paradigms. Public acceptance is, of course, required, so we have Formula E (now well-established) and perhaps other motorsport championships (Roborace, etc) and exciting points of engagement will be coming. EV vehicles will require new considerations. For example, EV driver/occupants will need to be presented with coherent battery management strategies so that terms such as ‘range anxiety’ are not only mitigated, but eliminated altogether. Simulation will lead the way on these efforts.
5. Coping with a new car interior
Car interiors are changing, and the vehicles being developed in labs and car clinics in 2018 will be on our roads in the next three to four years. Featuring greater autonomy, creative designers are already developing a step-change in how we deliver/receive information to/from the car. Gesture recognition, haptics and AI are already being trialed to see what works best for scenarios such as handing over from autonomy to driver, mobile office applications, or how good the car is at determining if you are alert. Testing and reviewing how we cope and what is not distracting or dangerous should always be done in an engineering-class simulator, so that realistic man-machine interactions can be explored. With dashboard tooling easily costing millions of dollars, no one wants to choose the wrong layout.
6. Safer testing
Comprehensive vehicle shake-down testing at trusted venues such as the Nürburgring Nordschleife are inherently dangerous and accidents with prototype cars are not unusual. As such, car manufacturers are increasingly looking at their duty of care to employees: testing anywhere outside sequestered proving grounds facilities is costly, expensive and dangerous. We are seeing more car makers using driving simulators to prepare their drivers for Nordschleife, winter test facilities, and so on, so that drivers can arrive prepared at the real facilities ready to make the most of their time there.