Italdesign and Williams Advanced Engineering (WAE) recently formed a partnership to provide the upper premium automotive sector with a complete, high-performance EV production solution. The platform will combine a composite electric vehicle rolling chassis from WAE, coupled with turn-key vehicle development services from Italy’s Italdesign. ATTI speaks to Dyrr Ardash, senior commercial manager, Williams Advanced Engineering, to find out more.
How has the EV platform evolved since WAE’s initial EVX concept?
When we brought out the originally EVX. That was very much a design concept study as to what could be achieved, and there were elements which weren’t necessarily appropriate for [production numbers of] more than 10s of cars. We did a lot of market research to ascertain what we wanted to do next. One of the important requirements we identified was that it can’t be just a skateboard, you need to be thinking about the appropriate integration with the top hat. One of the other key points that was very clear was that a platform can mean different things to different people.
Can you give an example of this?
Let’s say you’re a startup and you’ve got no automotive background, or a technology organization that wants to create a car from scratch, which is happening more and more. Between us and Italdesign, we could create an entire vehicle from scratch. Or alternatively, at the other end of the scale, you might be a manufacturer that only wants a structural battery.
Do you develop your own design and simulation tools in-house?
It’s a combination of three approaches. If it’s appropriate, an off-the-shelf tool set from one of the CAE suppliers will be utilized so long as it fits our needs well. Sometimes we make requests for modifications, specifically against our requirements, and they will normally accommodate those.
Then there are some tool sets which are completely WAE, where we just couldn’t find anything on the marketplace and have needed to develop them, which we view as a specific USP for us. For example, looking at batteries, that’s definitely somewhere where we have our own unique toolchain from a simulation perspective.
Can you explain more about your approach to battery simulation?
We take a physics-based approach to battery development and go into a lot of detail in terms of modeling at a cell level. Rather than just thinking about the cell as a block of material, there’s a lot of detailed modeling to find the marginal gains, that’s where we think that there’s opportunities.
We’re not just a battery supplier, we don’t just engineer batteries, we understand the system of the battery, but we also understand the system of the battery in the larger context of the vehicle powertrain. And I think once you do that, you can unlock a lot of further benefits as well.
What physical testing do you conduct on batteries and powertrains?
When you look at the various different projects we have undertaken, with OEMs and in motorsport, the breadth of our experience and understanding is quite significant. We have cell testing capability in house and we utilize the appropriate partners as well, MIRA, Millbrook and various other organizations.
Sometimes we completely manage the testing, because it might be right at the cutting edge, or we oversee the testing, giving the test specification and the requirements to the test house. We would rarely get them to manage the testing in the sense of doing all the reports, because we want to look at and oversee the data ourselves, and make the appropriate assumptions. Sometimes we take an approach that is quite different to what traditional OEMs might be doing.
How have you gone about validating the composite chassis for production?
We’ve worked with the supply chain on that. We’ve got a fairly experienced Tier 1 who would be the production partner in this area. From a manufacturing consistency perspective, we leave that responsibility to them, but we’ve worked with them from a DFM (design for manufacturing) perspective, which has been quite a detailed process. Obviously we’ve done the appropriate sample testing, we do quite a lot of CAE correlation, so that we don’t have to keep making stuff, that’s definitely an important element.
Does the company’s motorsport background give it an advantage compared with traditional OEMs when it comes to composite engineering?
Absolutely, it goes back to utilizing the experience and the expertise internally, the tool sets where appropriate, but also knowing when to go into the supply chain, where there are some really good specialists in these areas, and utilizing them. That’s maybe not an approach that a traditional OEM would have historically taken.
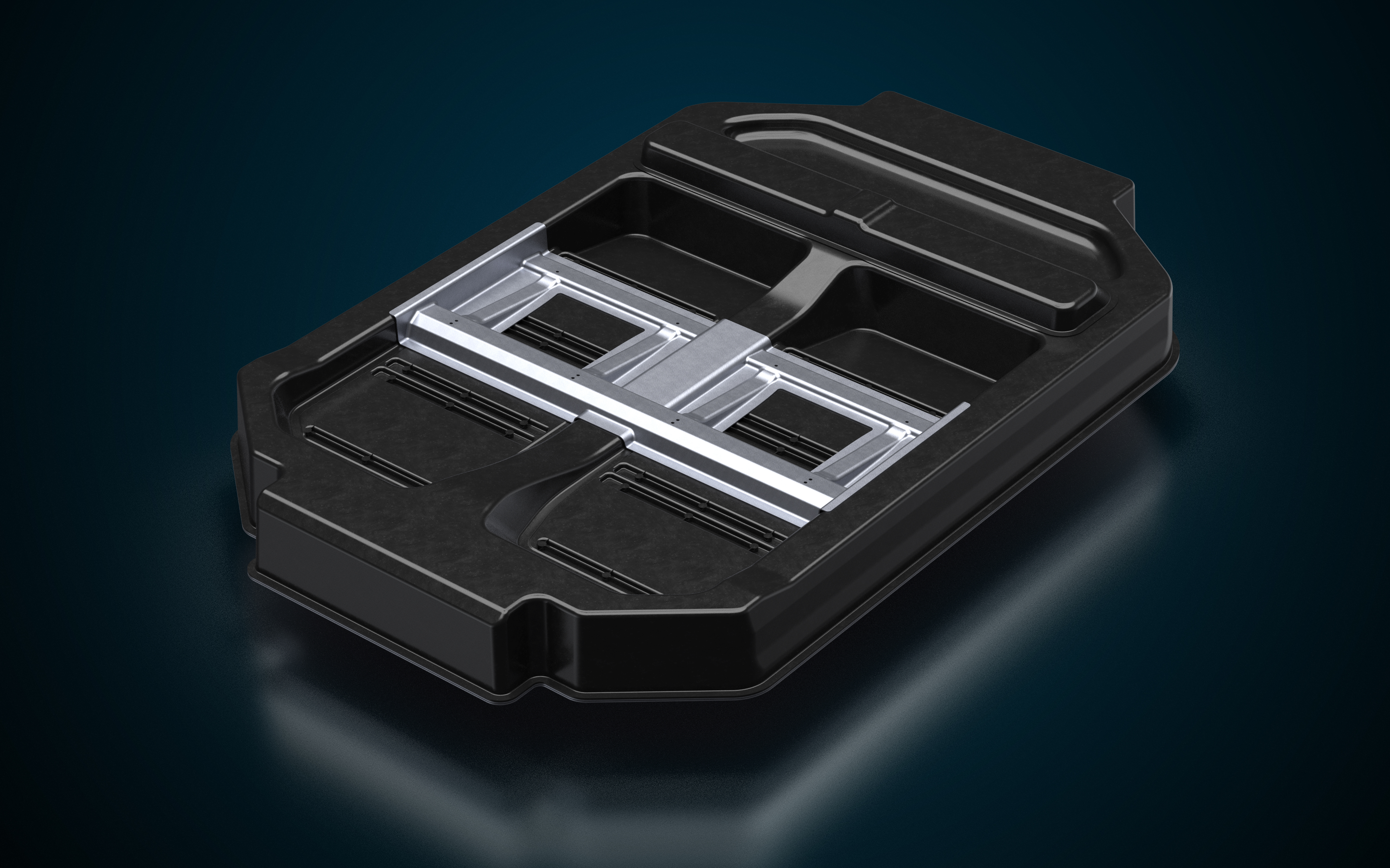