ATTI investigates how the Praga Bohema’s simulation program went to new lengths, beyond the bounds of what was originally planned
In March, Czech brand Praga reported that the last phase of development for its road-legal hypercar, Bohema, had commenced. The program for the company’s latest creation threw up a multitude of technical, creative and intellectual hurdles. The vehicle’s carefully crafted aero package and its performance credentials are the result of an intensive virtual strategy that ended up playing a greater role than was initially expected.
Much of Bohema’s design language, including the shape of the car, came off the back of CFD simulations. According to Jan Martinek, project leader and chief engineer, “In the initial stages there were a lot of feedback loops – going from a clay model to a 3D scanned shape optimized for CFD and back to clay to find a functional design that doesn’t lose its distinguished and potent combination of form and function.”
CFD was also used heavily when honing the hypercar’s performance as the team strove to get the maximum out of its package. Major emphasis has been placed on the interaction between vehicle dynamics and aerodynamics.
Virtual tools employed included TotalSim, Icon CFD software, ChassisSim, OptimumG and Ansys. According to Martinek, Praga believes these are some of the best-value platforms available on the software market.
Software aside, known quantities could be relatively easily simulated, such as the structural integrity of a part bearing a defined load or the behavior of air when presented with the dynamic conditions of a fixed body design.
“What is harder to simulate are the things you don’t know – the HVAC system, for example,” Martinek says. “The Bohema interior is quite compact, hence the packaging wasa real challenge. It effectively meant that pretty much all components had to be designed bespoke.
“The HVAC system had to be defined very early on as it takes up a big volume of space, when most interior components and even major features such as the seats and center console did not exist. Luckily, the conditions we modeled in the early simulations proved mostly correct, meeting the packaging [requirements] and only requiring a minor correction to optimize the air flow.”
Four dimensional
The real-world testing portion of the program was split into four elements: composite structural testing, engine analysis, wind tunnel evaluation and performance validation.
Novel manufacturing techniques have been applied throughout Bohema’s structure, and these had to be assessed thoroughly. “We tested samples of composite materials and layups. We have integrated Zylon panels into the car’s structure and we have done a lot of manufacturing optimizations,” Martinek notes. “We also tested flexibility as [the car has] one of the widest mounted rear wings [in the industry] and it’s important to understand the wing’s behavior under aerodynamic loads.”
This was the first time that the current team at Praga had to address emissions standards as harsh as Euro 6d, which Martinek admits proved to be a challenge. In-depth engine scrutiny and code writing were critical to achieve the stipulated values.
At Praga’s development center, engineers can use an engine dyno and rolling road. The OEM also has close ties with the Czech Technical University in Prague and the Brno University of Technology, where a raft of other resources are available.
Furthermore, Praga owner Tomas Kasparek has long-standing relationships with members of F1. This meant the team were able to access a Formula 1 team’s wind tunnel, which gave them an opportunity to verify their CFD computation models and input new data. “It was great to be able to verify and sign off the final design with a wind tunnel report from engineers in F1, and also look at future options using our knowledge to decide where to go next with the package,” Martinek comments.
Three prototypes and two pre-production prototypes were fabricated. For a bespoke company like Praga, which plans to make just 89 cars, that is sufficient.
Bohema has been assessed on airfields, racetracks and public roads across Europe. The majority of track and public road analyses took place in Slovakia, at and around the Slovakia Ring, with which Praga maintains a strong connection, meaning engineers can test there more or less whenever they need to.
“It is a great track for testing as our development and carbon center is nearby, so we can regularly access [the track], which has a technical and fast layout,” Martinek says. “The roads [in Slovakia] feature a perfect combination of new, smooth asphalt on the highways and very poorly maintained rural back roads.”
Track work was split into two parts: endurance and performance. Analysis on racetracks began back in 2019. During the last leg of Bohema’s development, the team dedicated a year to public road testing.
It’s not clear-cut
Martinek says it’s impossible to draw a line between how much virtual and how much physical testing has been done, because the simulation regime became gradually more iterative throughout the hypercar’s engineering. “There was a period at the beginning of the project when there was a true mix of best practices – with simulation playing a supporting role – because the original team behind Bohema was made up primarily of people with vast practical experience but comparatively little simulation background,” he explains.
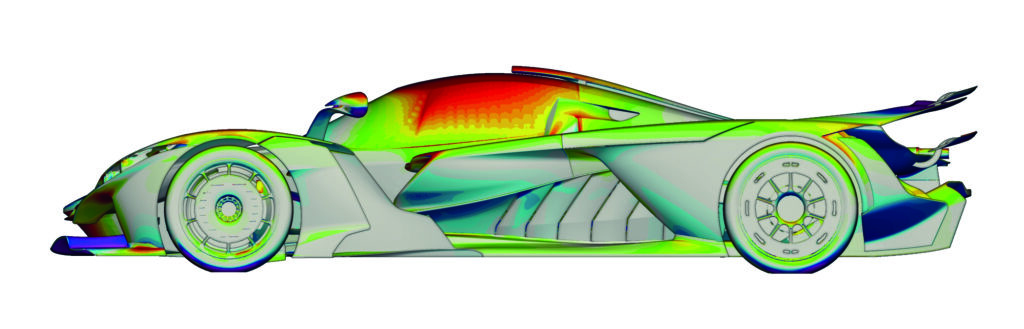
and modeling
This approach slowly transformed, with Bohema’s design becoming more heavily influenced by virtual analysis as the days went on. During the latter project stages, the team employed digital tools where possible to make refinements, squeezing out those all-important cumulative performance enhancements from Bohema’s package – the role and capability of simulation growing all the while.
“Looking back, the virtual portion of the program ultimately grew way beyond what we originally anticipated, yet very little of the original overall architecture had to be changed. This alone is a strong statement that evidences the know-how within the Praga team. However, the significant, incremental performance upgrades we were able to make through further simulation and optimization is as good of a statement on current simulation software power and necessity,” Martinek concludes.
Puzzle to solve
To define the vehicle dynamics characteristics of the hypercar, overall performance targets were set first and an understanding of the tire established, Martinek explains.
“Then we started putting the pieces of the puzzle together. We used tools for simulating tire performance and the behavior of the car in terms of the vehicle dynamics and aerodynamics to achieve our targets.
“We were then able to simulate the ideal aero balance during different situations on the track and maximum value of downforce to not overload the tires, and so on.”
Interestingly, Pirellis proved to be far more effective on the car than any other brand, Martinek notes.
“Once happy we had achieved the targets, we used this data in simulations of
the structural parts, enabling us to determine theoretical loads and optimize the parts in terms of stiffness and weight.”