With a number of electrification projects under its belt and more in the pipeline, UK tech company Sprint Power is pursuing an ambitious growth plan. ATTI takes a tour of the company’s UK base.
Established in 2018 as an engineering service provider, over the last 12 months, the UK firm has broadened its capabilities to encompass the development of niche battery solutions. Modular, lightweight and cost-effective, these solutions are designed for next-generation applications, and include battery management systems, power electronics and DC/DC converters.
Founder and CEO Richie Frost says, “We keep our finger on the pulse with what’s being developed in the electrification arena, and build our products so they can be applied with the very latest technology. We maintain a close relationship with suppliers including cell manufacturers.”
According to Frost, by being agile and adaptable, Sprint Power can help its clients reduce their project timelines. Its UK base houses an engineering office, a prototyping lab and test equipment such as dynamic power supplies, load banks and climate chambers. The company also has a manufacturing facility close to Silverstone where it can build prototype parts. Having direct access to these resources enables engineers to trial new ideas in an instant.
With growth high on the agenda, in 2020, the supplier effectively doubled its team to almost 80. An aggressive recruitment drive aims to double that figure over the next year, with on average, four new engineers being taken on each month. That includes graduates through to directors.
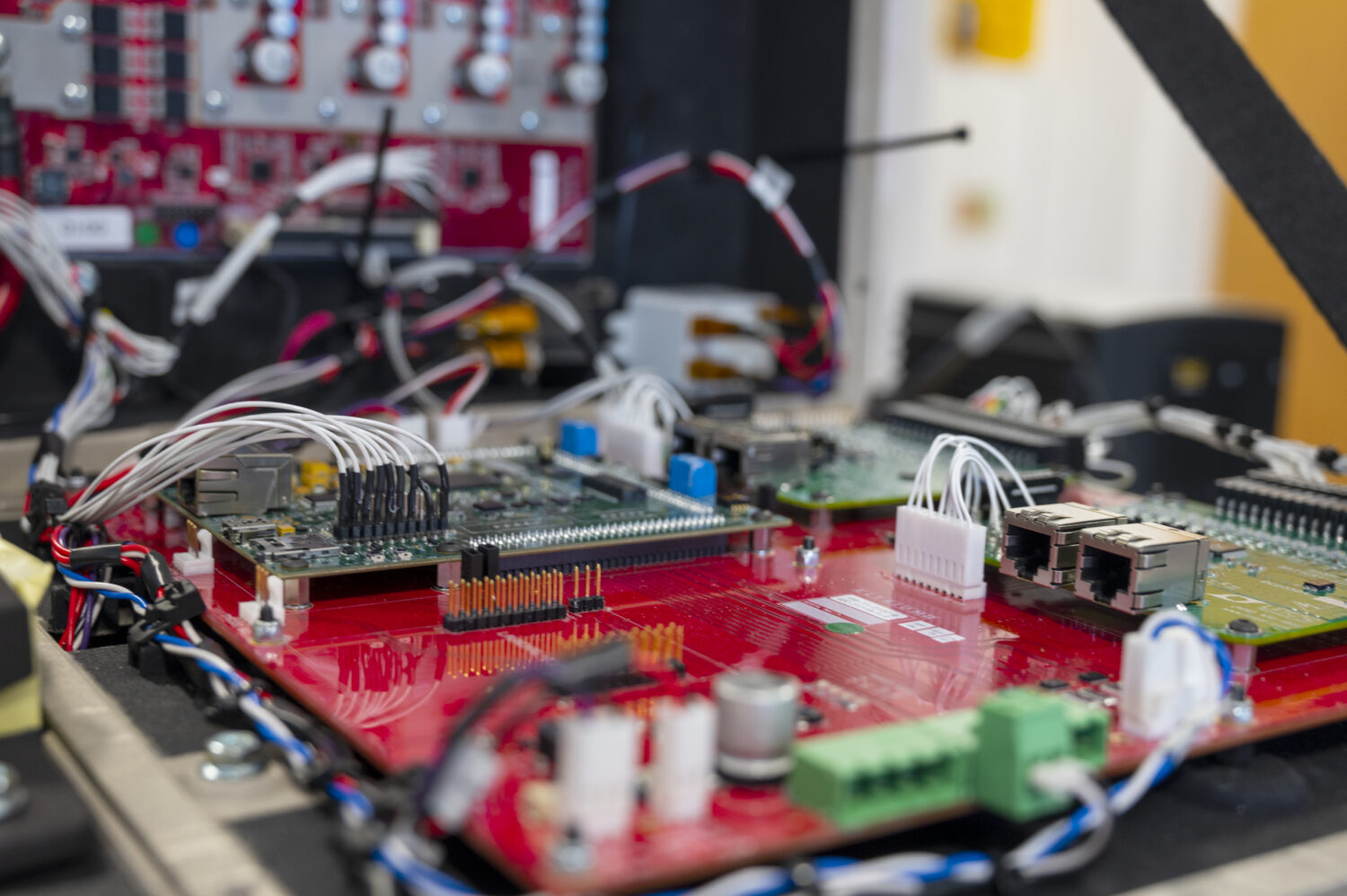
Alongside this, new departments and roles are being created within Sprint Power to cater for the breadth of future projects it is now involved in.
Frost reckons that a central reason why automotive developers approach his company is because of the company’s wide range of specialisms, from systems integration and battery systems to power electronics and controls, all under one roof. Frost also believes that skilled engineers nowadays prefer the fun and flexibility that startups such as Sprint Power can offer, and the diversification of its projects, which is often very appealing.
“Recruitment in this sector is extremely hard, and I set Sprint Power up with the mindset that there is going to be a significant skills gap in the UK for a number of years. I’m deeply inspired by the cultures of tech companies in Silicon Valley, and at Sprint Power, we want to create an engineering playground where we can recruit the best engineers. In the UK, and especially in the Midlands, there’s an enormous demand for the same specialists, so we have to have a future-focused strategy around developing people.”
“As an employer, it’s crucial to ensure that assignments are interesting and exciting”, Frost adds. “With around six projects going on at any one time, each team member is involved with several projects, and that can mean working on anything from sports cars to race cars to super yachts to boats to planes to trains, in the hydrogen, hybrid, fuel cell and autonomous arenas. We want to offer a fun working environment that’s very accessible, innovative, open and flexible.”
When it comes to recruiting, it’s as much about the individual’s personality as it is about their qualifications, according to Frost: “We need the right people with the right skills, but also the personality and mindset; a candidate must be self-motivated, passionate, and share our enthusiasm for electrifying things as well as our excitement for the growth of the business. It’s about having that ‘get up and go’ ethos.”
Q&A: Steve Doyle, chief engineer, battery systems, Sprint Power
What is Sprint Power’s approach to electrification in the automotive market?
Hybridization and electrification are the biggest market drivers currently. In terms of battery systems, we are working on developing combined packages. The various elements of a battery system are normally separate; however we have been working to integrate them. In a 48V vehicle, for example, you have the 48V battery, the 12V battery and a separate DC/DC converter, which would be sourced from different suppliers. We’re able to integrate those systems while making the overall solution smaller, lighter more cost-effective and more efficient, while improving the functionality.
What are the current electrification trends?
We’re currently looking at developing 800V systems so that we can not only service the hybrid market, but also the EV segment.
A few years ago, the prime issue was range, but now that has been addressed, the focus is switching to charge time. For both EVs and fuel cell-powered vehicles, which are beginning to enter the mainstream market, there is a requirement for the batteries to be able to cycle at a much higher rate, enabling a vehicle to be charged faster. As such, the industry is working to develop battery cells and technologies that can cope with this.
There are currently only one or two cells that can do ultra-fast charging, and all the subcomponents are currently qualified for 400V, so it’s not just a case of finding a cell that can charge faster, it’s about qualifying all components to run at 800V.
DC/DC converters are increasing in ratings from 800V to 1,200V, and in order to cope with these high-power ratings, the industry is using silicon carbide. Switching devices are also changing, so we’re working with other suppliers to put a silicon carbide device into a new DC/DC converter.
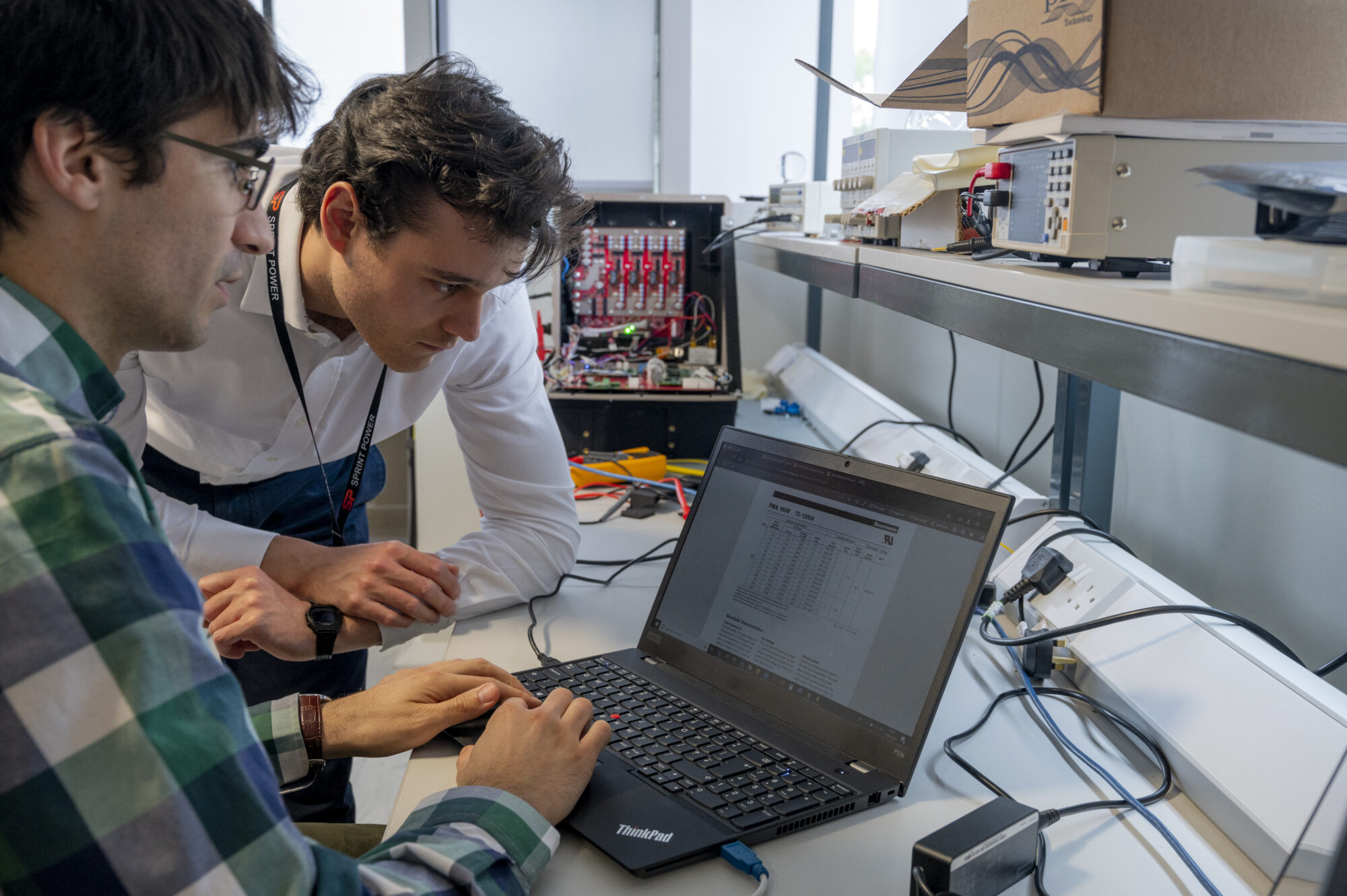
With early EVs, the onboard charger talks to the battery and the plug-in charger. The industry is working to incorporate that into the BMS as part of the charging protocol, but this is complicated as there isn’t just one charging protocol.
At Sprint Power, we’re also assessing wireless charging and the conversion of conventional vehicles to wireless charging. The knowledge that we put into that black box for conversion will be built into our next-generation BMSs.
How fast is the rate of change in innovation in the sector?
The battery industry works on a lifecycle of around three to five years. Development of a vehicle could take around the same, so you’ve almost used the lifecycle of that cell in the development cycle of the vehicle. In the second or third validation phase of a project, we may therefore need to swap the battery cell we’re using for the most up-to-date cell. This rate of change is unlikely to slow down.