Dewesoft offers a single system for efficient measurement on the road with exportation of data to a road simulator as well as recording on a rig
Durability testing of all major components is an important part of the vehicle development process. Simulations of stress and strain can help find and predict major failures even before the prototype phase, but the main process begins once the vehicle is ready for real-world testing. There are two common ways to test whether a vehicle will be able to achieve its set durability target: through testing on a real road or through simulation on a road simulator. The latter can be done with the complete vehicle or for subsystems or components, which makes the complete testing process faster and easier.
When testing a complete vehicle, the process starts by equipping the vehicle with sensors and measurement equipment. Strain gauges and load cells are used on all major suspension and chassis components. Wheels are replaced with special wheel force transducers (WFT), which have integrated load cells in the rims and can measure forces in all three directions.
It is also important to measure certain data directly from the vehicle; for example, steering wheel angle, which is available over CAN and Flexray. Furthermore, GPS information can expose exactly which parts of the road tested caused a certain response; having video recordings along with all this data also helps visualize the test in the office.
The struggle is in combining all of these measurements. Recording data with several systems, one for WFTs, one for strain and acceleration, and another for vehicle bus data, poses the challenge of how to combine it into a single measurement for easier analysis. Everything can be measured separately and then imported and manually aligned, or data can be sent over CAN to a single system with potential delays in data transmission.
Dewesoft offers a solution to record everything with a single system fully synchronized. The company’s
data acquisition devices have native support for analog inputs for strain gauges, IEPE accelerometers and load cells. With the Kistler KiRoad or RoaDyn support, the wheel force transducer data can be added and fully synchronized with the data acquisition system. Other WFT systems can also be connected using CAN, and all channels are delayed automatically by measuring and entering the delay. Dewesoft also offers native CAN FD support and supports Flexray, LIN, SENT, XCP, CCP and many other digital buses.
Once the measurements on the road are complete, the process of analyzing the data and creating replay files for the road simulator can start. DewesoftX software can export data in RPC III format directly for testbed use. Analysis can be done in the software or data can be exported to one of many available formats that are compatible with all major analysis tools.
Traditionally, two systems would have been used on the road simulator: one for data acquisition and another as a signal conditioner for the feedback loop for the testbed controller. In the past, this was replaced with a single system that could measure strain, stress and acceleration, and store all the measured data, while also working as a signal conditioning unit able to output every analog input through an analog output directly to the testbed controller. However, this meant that every signal needed a separate cable – an enormous amount of cabling.
Dewesoft’s R4rt unit solves several problems at once. The system has a so-called dual mode in which it can capture and store full-speed analog data from load cells, accelerometers and strain gauges and at the same
time send data to the testbed controller. The link to the controller no longer requires separate analog lines as it did in the past; instead, it just needs a single EtherCAT line. The cost saving alone – no longer having dozens of long analog lines – is huge, but the greatest benefit is having a reliable, noise-free signal.
Thanks to the R4rt unit’s compatibility with MTS, Instron and other controllers to receive EtherCAT data, testing is easier for those developers already using this solution. Undisputable data can be obtained as the same system can be used out on the road and on the road simulator. This also drastically reduces the time needed to instrument the vehicle for both types of tests.
The system offers many additional features that improve the quality of results. Filters available on real-time EtherCAT data can prevent the controller getting implausible values. Unlimited system expandability from eight to thousands of channels makes it suitable for testing small components up to full vehicles with a high number of sensors. At a sampling rate of 1MS/s per channel, it can record even the shortest events.
DewesoftX software is constantly being evolved and new features added, all without any additional cost
for the customer. Furthermore, with no hidden costs or support and service fees, the system is very cost-effective.
More information can be found here:
https://dewesoft.com/applications/vehicle-testing/road-load-data
https://dewesoft.com/applications/vehicle-testing
* Sponsored
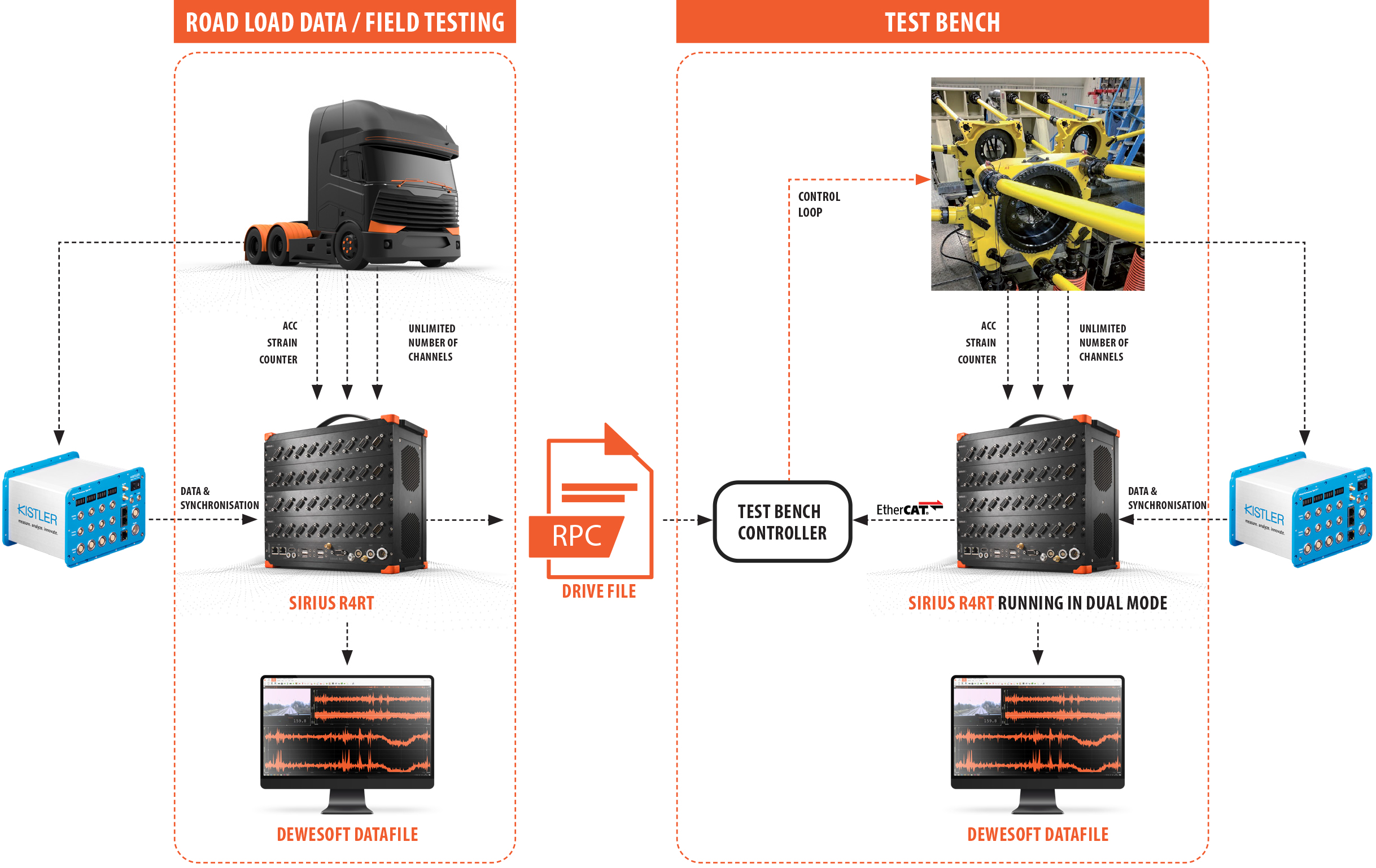