Advanced solutions from eMpulse Test Systems that incorporate Siemens motion control and automation components offer the company’s customers much more precision and accuracy with up to four times greater frequency response plus energy savings of 80% or more compared to legacy servo-hydraulic equipment
Since the early 1980s, the automotive industry has used hydraulically actuated (servo-hydraulic) test systems to simulate operating speeds and road conditions for testing OEM components and fully assembled vehicles. They have helped unlock vast improvements in the quality, safety and reliability of the cars and trucks coming off the world’s assembly lines.
Thanks to these four-poster road simulators, vehicle manufacturers and their suppliers nearly eliminated the buzz, squeak and rattle (BSR) issues that once could plague new cars and trucks, annoy their owners, and cause huge headaches and costs for dealers and manufacturers alike. Other vehicles – motorcycles, ATVs and golf carts among them – are now tested similarly. Durability testing; noise, vibration and harshness characteristics; and accelerated life testing can all be assessed.
Servo-electric test systems with next-generation digital technologies
Today, electrically actuated (servo-electric) test systems have emerged as a preferred alternative to servo-hydraulics that have traditionally been used. Michigan-based eMpulse Test Systems is a leading supplier of these advanced testing systems. The company uses servo-electric actuator (SEA) technology in its four-poster road simulators, and has more than 200 worldwide installations with all the top vehicle manufacturers. The rapid growth in electric vehicle production favors these systems over legacy servo-hydraulic ones, as do environmental concerns.
President and CEO Matthew Johnson explains that SEA-based technology offers increased precision, higher performance, and more energy-efficient and environmentally friendly simulation testing. “Compared to servo-hydraulic systems, servo-electric actuators let manufacturers more precisely and accurately conduct a wide range of test applications including durability, accelerated life, NVH and BSR,” he says.
“In fact, our SEA test systems use less than 20% of the energy that servo-hydraulic systems do, thereby reducing their energy costs and carbon footprint by 80%. Plus, they’re extremely clean and can’t leak hydraulic fluid into the environment.”
In addition, the company’s broad portfolio of test equipment includes SEA-enabled multi-axial simulation table (seaMAST) systems, that can apply force and motion in as many as six degrees-of-freedom. “These systems simulate complex dynamic motions by replicating the stresses, strains and vibrations products may experience in real-world environments over their lifetimes,” Johnson says.
Challenge: To maximize the accuracy, responsiveness and reliability of its servo-electric testing systems
According to chief technology officer Doug Boals, the development of the eMpulse Test Systems SEA-based road simulators and seaMAST systems required motion control and automation technologies of the highest quality in terms of performance, accuracy and reliability.
“Linear motors are the primary components in our systems’ actuators,” he says. “So, we needed ones with well-integrated companion drives to have high continuous force ratings that could ensure our customers can execute the broadest range of test applications possible. Our customers also needed our systems to be rated for continuous duty cycles for their R&D and durability testing procedures.”
For example, Boals notes that the extremely precise control of the motion in the company’s SEA-based test systems is especially important to automotive manufacturers because they increasingly want to replicate diverse sets of road conditions, including surfaces, topologies and weather conditions.
“Many go out and laser-map various roadways with the goal of reproducing the different types of roads, whether they’re asphalt, jointed concrete, rumble concrete, Belgian blocks or other pavement types, and even potholes,” he says. “Servo-hydraulic systems can’t reproduce higher frequency events because the oil in their lines acts as a cushion. Our servo-electric actuators use motors and drives that deliver a frequency response much better than those systems.”
Boals adds that reliability and easy maintenance were other design and engineering goals for its test systems. “Of course, unplanned downtime is always disruptive to testing throughput and can affect production, too,” he says. “Every minute of downtime, unplanned or planned, costs money, so we wanted to give our customers test systems with rock-solid reliability and less maintenance to ensure they get the most asset utilization, uptime and availability possible.”
Solution: Standardize on Siemens motion control and automation components
In choosing a source of their motion control and automation technologies, Johnson, Boals, and the company’s engineering team, wanted more than a supplier. They sought a strategic global partner with industry experience; proven, highly integrated components; and worldwide support and service. They chose Siemens and contacted Electro-Matic, their local value-added Siemens distributor.
Johnson recalls their decision process: “We considered many other suppliers, but Siemens’ product capabilities were better than our alternatives, plus their strong global presence within the automotive industry and reputation for quality made it an easy decision.
“Importantly, with the Siemens distributor network spanning the world, our customers can count on local support. If downtime occurs, they can be up and running much faster than it would take us to fly one of our representatives to them with spare parts.”
As the company’s CTO, Boals offers his view on the Siemens portfolio and technologies: “Siemens has a wide range available hardware which enables us to easily size our road simulators and seaMast systems to a customer’s specific application requirements. eMpulse proprietary configurations enable us to increase the performance of our servo-electric actuators far beyond what other suppliers’ servomotors can deliver. This allows eMpulse to offer unique durability and endurance testing solutions.”
Flexibility for customized test solutions
For motion control, eMpulse has integrated various servomotors into the Sinamics S120 modular servo-drives from Siemens. The drives offer vector and servo functionalities, including multi-axis capabilities, that support both the road simulator and seaMAST test systems. “The Siemens products give us tremendous flexibility in tailoring test solutions to our customers’ needs,” says Boals. “They also provide high dynamic performance, precision, compactness and ultra-reliability.”
The electrical actuator assemblies in these systems include absolute (not incremental) high-resolution optical encoders. These provide an internal resolution to the motor controls of 1nm, with a <10nm resolution available for data analysis. eMpulse uses its own proprietary servo-controller with customized GUI for various testing applications. Its controller digitally communicates to the Siemens drive system using Profinet, a high-speed isochronous real-time ethernet communications protocol.
All internal drive parameters and signals are thereby available to the control for monitoring, control and diagnostics, without inducing electrical noise that is inherent in typical analog-to-digital and digital-to-analog interfaces used in competitors’ products.
“Siemens supported our starter project programming to get our early systems online faster until we were able to gain our internal expertise in starter programming and the Totally Integrated Automation (TIA) Portal,” Boals says. “Today, the TIA Portal saves us lots of time and effort in programming the different Siemens components and integrating our proprietary code into their operation.”
Built-in safety to protect personnel and equipment
Simatic controllers are failsafe models with integrated motion control, command processing cycles as fast as 0.125ms, and safety integrated. The latter can safely stop drives and safely monitor motion in accord with SIL 2 (EN 61508) and Performance Level d (EN ISO 13849-1) standards.
“Safety is a vital functionality in our test systems,” Boals says. “We use the Siemens Drive-Cliq interface and Profinet connectivity to continually monitor our motion encoder signal in real time to assess the integrity of its position feedback. At any time, there’s an encoder misread error, our systems can stop motion within a millimeter of a fault condition. That’s much, much safer than a servo-hydraulic system.”
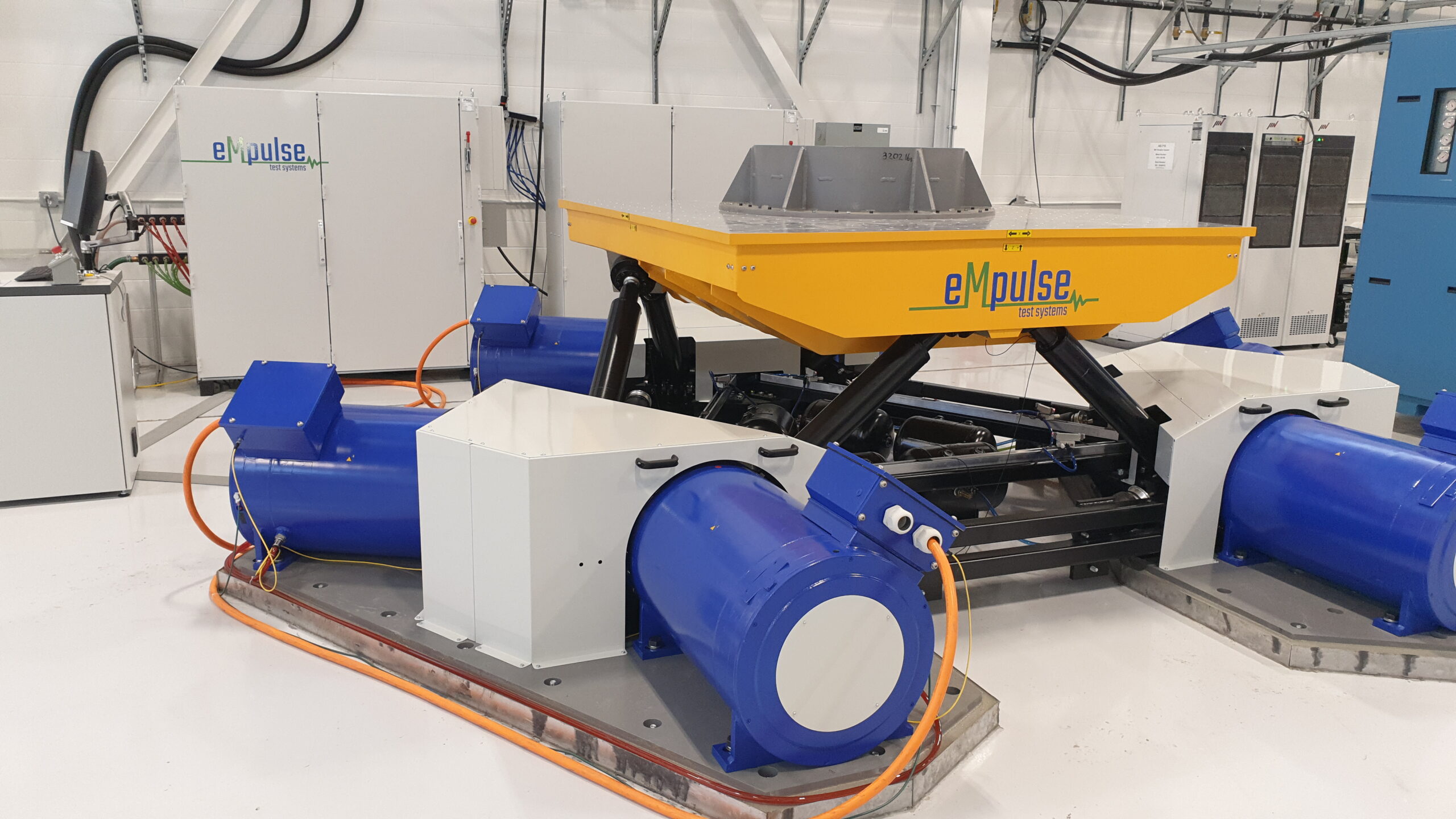
Results: More reliable, advanced test systems with smarter performance, more efficiency, and greater sustainability
By standardizing on Siemens motion control and automation components, eMpulse Test Systems can now assure customers that their road simulators, seaMAST, and other test equipment will provide the best performance, efficiency and reliability possible – all in support of more sustainable and environmentally friendly operation than legacy servo-hydraulic test systems.
“For example, with Siemens motors being liquid-cooled, our test systems can more effectively remove heat that would otherwise limit the continuous force ratings of other motors,” Boals says. “In addition, liquid cooling provides much faster recovery from peak loads, which translates to higher duty cycle usage and more uptime.”
In turn, these performance enhancements have expanded the testing capabilities of the company’s systems. “So, our customers can conduct durability and accelerated lifecycle testing on automotive parts or OEM sub-systems by running cyclic tests continuously for days or weeks to determine their failure modes,” Boals explains.
Up to four times more responsiveness and control
Compared to legacy servo-hydraulic testing systems, the company’s SEA-based systems deliver more intelligent testing with a much greater frequency range, especially at the high frequencies needed to detect more nuanced simulations of road conditions. “We use our own proprietary, high-speed digital communication hardware module that connects directly with the Siemens components via Profinet,” Boals says. “This eliminates the noise and inaccuracies inherent in analog control schemes.”
The improved performance and frequency response of the eMpulse test systems has enabled its many customers to identify quality issues that were previously undetected using older technologies. “In fact, the frequency response of our linear motors is three to four times better than what servo-hydraulic systems can provide,” Boals says. “This makes a huge difference for our customers in their testing because they can draw much greater fidelity from the data and replicate higher frequency events on our systems’ four posters with better accuracy and precision.”
Energy-savings of 80% or more, lowering total cost-of-ownership and improving sustainability
Servo-hydraulic testing systems lose tremendous amounts of energy by needing to be operated in standby mode, having to pump hydraulic fluid often from hundreds of feet away, and line losses on the return side due to fluid back pressure. In contrast, eMpulse SEA-based systems only use energy when testing is conducted, thereby reducing energy use by 80% or more.
“Energy-savings are a big deal because our customers can avoid hundreds of thousands of dollars in utility costs over a 10- to 20-year operating lifespan of our equipment,” Johnson notes. “The savings can accelerate our customers’ returns on investment and lower their total cost-of-ownership.”
Less energy use also translates into an improved sustainability profile for customers by reducing the carbon footprint of their operations. Sustainability is an important company value for eMpulse Test Systems, aligning it with the sustainability values of its customers.
More reliability for greater asset uptime, overall equipment effectiveness, and utilization
Johnson and Boals consider the Siemens motion control and automation components as key factors in simplifying the operations of their test systems. “Siemens components, in particular, have greatly reduced the possible failure modes when compared to other technologies,” says Boals. “This means our customers can expect more system uptime and availability, which can improve their OEE (overall equipment effectiveness) and asset utilization metrics. For shareholders, improvements in these metrics ultimately translate into greater returns on capital equity.”