Gordon Murray Automotive, which was founded on the principles of cutting-edge motorsport engineering, is setting zealous goals for its emerging ultra-exclusive sports cars, as group CEO Phil Lee explains
Few startups have arrived to expectations as grand as those behind Gordon Murray Automotive. Spun out of Gordon Murray Design in 2017, it’s a brand rooted in over half a century of race-winning innovations, taking a similarly uncompromising approach to its own model range. All 100 examples of the company’s first product – the T.50 supercar – sold within 48 hours and, with the setup of new premises, an ever-expanding workforce and development of the T.33 underway, group CEO Phil Lee sees no room for the company to rest on its laurels.
“We’ve got cars planned out all the way up to 2033 and, no doubt, [Gordon Murray] has ideas that go up
to 2035 and beyond. He’s designing prolifically. I’m excited about everything that’s associated around the challenges that that brings,” he tells us. “We wanted to make sure that, especially building the brand, the first product was exceptional.”
Lee joined the company in 2019 as its first employee. Bringing more than 20 years of expertise from firms including LEVC and Lotus, his role has involved building most of the infrastructure for the incoming model range from a blank sheet of paper.
In its first 12 years, the Gordon Murray Group had amassed a workforce of 90 employees at its UK head office in Shalford, Surrey. Three years later, there are 260 people working across its three divisions – Gordon Murray Automotive, Gordon Murray Design and Gordon Murray Electronics – and construction of
a £50m (US$59.4m) headquarters and tech campus is underway in nearby Windlesham.
“You would think that, with such a large volume of people joining, the culture starts from the newcomers,” Lee continues. “What actually happens is the culture originates around the center, and the people you recruit in the key positions. They recruit people of like nature, and therefore it mushrooms out. You have to recruit the right people, at the right time, doing the right role not just in terms of competency, but the mindset of the organization.”
Bold moves
Company founder, Prof. Gordon Murray, is a linchpin of an engineering process ruthlessly focused on reducing both the weight and complexity of group products. Vehicles are styled in collaboration with chief creative officer Kevin Richards, and translated to a vehicle architecture through detailed assembly drawings exploring every component. Lee says rigidly setting out functions early enables later stages of engineering and development to effectively offer confirmation of concept, which reduces complexity too.
With an appetite to try new ideas, the team relies on simulation to learn lessons early. Lee says this approach proved invaluable as teams switched to remote working during Covid-19 lockdowns in 2020, enabling the computer-aided engineering phase of the T.50’s development to carry on uninterrupted and for the workforce to continue growing.
In turn, construction and testing of the company’s first mule, a modified Ultima nicknamed George, began as restrictions lifted in the summer of 2020, featuring an early, rev-restricted version of the car’s 3.9-liter Cosworth V12 engine. Experimental prototype versions followed within months, introducing the carbon-fiber monocoque and aerodynamic elements.
Now undergoing the final phases of validation, the T.50 is distinctive enough that the company won’t be camouflaging prototypes. Its 40cm aero fan accelerates airflow under the car, reducing the need for visible ducts, vents and flaps on the upper surfaces. This is powered by a 48V electrical system, which also cranks and helps cool the engine and provides an additional 50hp to the wheels.
Weekly meetings during the regime have brought engineers together to scrutinize and strip weight from every component. The T.50 weighs just 986kg, but Lee says the engineers’ biggest headaches came from features such as the evolving electrical architecture.
“It’s the things that have been more complicated that I found quite interesting as a learning curve,”
he says. “As a business, a lot of the people here – the engineers – have learned a lot on how to approach programs. That’s not just from a technical aspect, but also from a peripheral side view as to what can happen with other ancillary systems.”
Although a lot of the expertise in architecture and control networks is kept in-house, early products have relied on external facilities for testing. Gordon Murray Automotive has a permanent and expanding base at Millbrook Proving Ground and, more recently, the team travelled to Nardò to put prototypes through climate and high-speed testing.
Only the best
In each case, employees all the way up to Lee and Murray have a hands-on role, finding and solving problems during development. Lee comments, “Anybody can raise a build concern report – from build, to development, to quality, to observation, to perceived quality. If that happens, the quality department assigns a department, a name and a date to close the case by. Our system is really about recording everything, and then trying to narrow that down and close [the case]. It’s designed to ensure we are not getting repeat errors and certainly not getting repeat problems. It’s about closing them, and closing them for good.”
Supplier specialism is a linchpin too. The automotive manufacturer claims that 90% of its components are UK-sourced, and it’s working closely with partners to ensure each element meets its strict benchmarks. Cooperating with Cosworth resulted in the compact and relatively small-capacity 3.9-liter V12 engine, designed to offer McLaren F1 performance levels and with a low-mounted crank to push the center of gravity as close to the tarmac as possible. The carbon-fiber monocoque, developed with Formaplex, includes an F1-style passenger safety cell and the bespoke Xtrac manual gearbox is semi-structural.
Its gearshifts were meticulously tuned for weight and throw, and were signed off by Murray himself.
“We punch above our weight with the supply base,” says Lee. “We have a lot of credibility, so we don’t have a problem, as you would probably expect with us being small, with not being able to get the interest of those suppliers. Quite the reverse, actually: they want to deal with us. I think because of our technical knowledge, we’re able to stay on top of those trends as things move toward more advanced architectures.”
It’s a foundation for ongoing evolution as the company’s product plans stretch further into the future. “We’ve had a lot of systems to implement and we’ve had to put them in from scratch. The T.50 was the catalyst but, once you’re on the train, you can’t step off. That means [you need] that investment in systems and also maturation of the organization through [those systems] to get control, because you
just become exponentially more complicated. We tend to use systems that are flexible. That way, hopefully they’ll grow with us.”
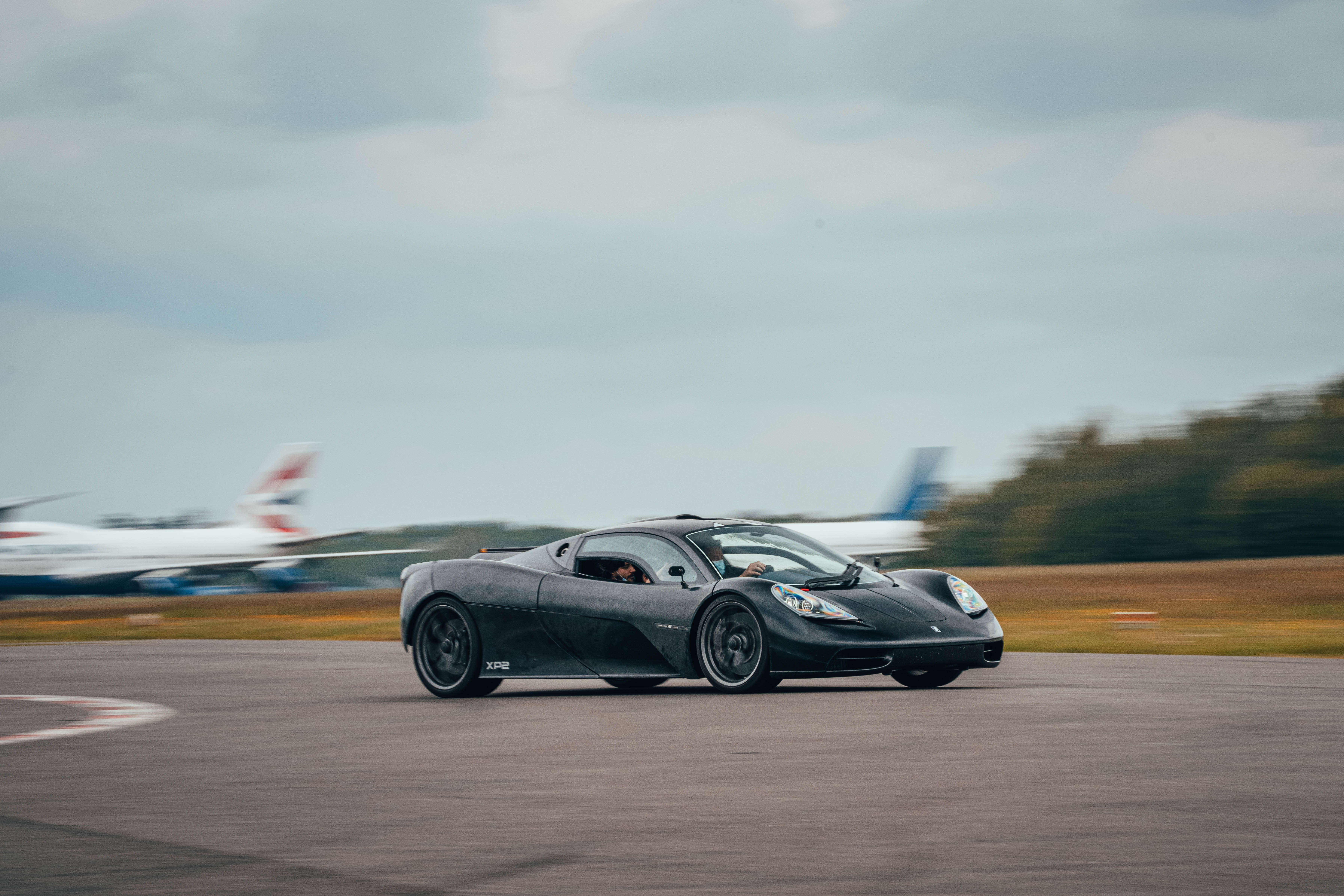
Fountain of knowledge
Although Gordon Murray Automotive is relatively small – Lee is quick to point out that the company will only ever build low-volume products for an exclusive client base – the wider group structure puts a vast array of competency within reach for future projects. Gordon Murray Design provides development and prototyping services, while Gordon Murray Electronics, which was formed in 2021, builds electrified powertrains.
Gordon Murray Group’s growing team is steadily moving to the new Highams Park technology center in Windlesham (below), not far from its current headquarters southwest of London, and it’s here that the T.33 supercar will be built. This 22ha site, acquired in 2020, also enables a more efficient R&D structure. Design teams will be located adjacent to individual prototyping bays and given access to
a shared engineering pool, and the site will include its own test track.
“On the other side [of the group] we can keep up to date with all the latest automotive trends, whether that’s cleaner powertrains, EV technology, connectivity or autonomy,” says Lee. “The group’s technology base has things such as structural batteries, electronics and electrical architectures, and they work for Gordon Murray Automotive but also external clients.”