Brian Jones, Hennessey’s newly appointed VP of engineering, discusses the philosophy of high-performance car development
Brian Jones, VP of engineering at Hennessey, is an engaging interviewee. Having been hired in September to spearhead the OEM’s hypercar development, overseeing all Hennessey Special Vehicles and Hennessey Performance Engineering projects, he hopes his vast experience will make telling contributions to Hennessey’s portfolio. That includes stints at auto and tire manufacturers as well as suppliers. Perhaps most relevant to his newest post, he had leading roles on the Ford GT and Mercedes-AMG One programs.
When the opportunity at Hennessey arose, Jones says it wasn’t a particularly difficult decision to make the move from Multimatic. It will allow him to exercise his skills on a fresh challenge.
“Hennessey is in a very interesting place right now in terms of its goals and the product plan,” he comments. “And it was a good fit for my interests. I’ve worked in the automotive and racing sectors, I started my career at General Motors and I’ve worked for Goodyear. I’ve also been the general manager of a wind tunnel, so although I’m a mechanical engineer I’ve always been interested in the aero side of things. Most recently I was with Multimatic, which does a mixture of projects.”
His job at Hennessey will be varied too. There are unfinished objectives on the current car – the Venom F5 – such as revisiting an attempt at the 300mph (483km/h) lap record, which is yet to be achieved. (The car was signed off at 272mph (438km/h).) Jones will thus spend much of his time getting to know the company’s halo vehicle as well as the team and the business in general.
In the longer term, Jones has been briefed with developing the new product line. It’s still in the early stages, so few details have been released, but we’re told it will definitely be an ICE car. Multiple variants will be built to appeal to a variety of consumers.
“It will likely have a manual gearbox and a slightly lower horsepower. It will have a different look and feel,
but of course there will be key elements typical of any Hennessey product.”
Certain charm
With his strong race and performance car background, Jones is certainly in the right place at the right time. It’s refreshing to know there are engineers who can turn their hand to just about anything, but even with all his experience, he admits there’s more to learn.
Yet more industry changes and challenges are on the horizon, and his know-how will be invaluable in helping the auto maker to flourish. Jones says that growth should be organic and happen at a rate that makes sense for the business to remain sustainable.
Naturally as the OEM matures, Jones expects there to be skills gaps, so more crew members will likely be brought on board. Meanwhile, he’s keen to ensure that the core current contributors continue to evolve and that they “feel like part of the growth process”.
Having witnessed other players lose a sense of self as they expanded, he believes it is vital to always remember the company’s bread and butter. “Growing too fast and not having all the right systems in place can result in an unhappy scenario. It’s about people and facilities, but there’s a fine line. Here there’s a strong objective to grow. Every company wants to grow and succeed, but I want it to be in a collaborative way and to happen at the right pace.
Working for a smaller manufacturer will afford Jones more freedom in building new vehicles than he’s had
in previous jobs. He’ll be able to use his experience to make judgments on a more abstract level without the constraints of defined processes like those that are adopted at large OEMs.
As Jones notes, low-volume car makers do not have the budget to recreate such a structure. More importantly, it’s not required. “When working with the OEMs you can get bogged down with their processes. And they all think their process is the best. Those processes were developed for a reason – they produce a lot of vehicles a year, they have a lot of warranty experience, and all that statistically works to help guide which processes work or show where there are shortcomings.
“We have a different customer base and our vehicles are intended for a different purpose. We have to find the right development process for our products.”
There are of course elements to a test program that are non-negotiable. However, as Jones notes, others can be approached from another angle: “There are things you can do with more rig testing, for example, or maybe you can do more testing at a full-vehicle level and less at a component level. You can make those decisions in ways that you can’t make at an OEM simply because their sign-off process won’t allow you to.”
Jones believes he has a unique perspective that will enable him to pick and choose what’s relevant for Hennessey. “For me, that’s the exciting thing – having experienced what everybody thinks works in their world, and having been involved through complete cycles from start to finish, I have the benefit of being able to see where there may be a case of rose-colored glasses.”
Jones’s initial task is to get familiar with the business, immersing himself in Hennessey’s culture, which is the essence of what makes it successful. He says, “When you come into a company you have to be sensitive to the fact that there are already people who have been working hard. The current car is very good. It’s been developed by this small team of hardworking individuals who have achieved a lot. It’s completely different from one of the most recent projects I worked on, which involved different budgets, resources and high-level OEM customer expectations.”
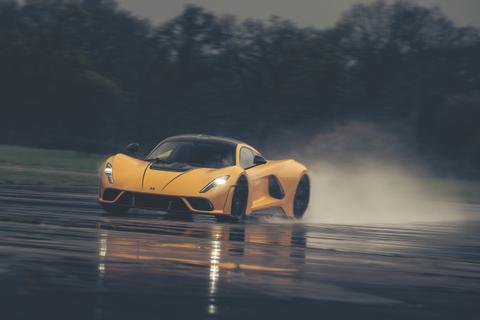
Study time
One area in which Jones plans to strengthen Hennessey’s testing armory is in simulation. For a company like Hennessey, virtual verification plays a different role from its use with a high-volume manufacturer. With much more flexibility, prototype components can be made on an as-needed basis.
Jones embraces the digital world, and as a top priority he aims to bring more simulation capabilities in-house. In what capacity is yet to be defined.
However, he believes that the learning truly starts in the physical realm. “Let me put two bookends out there,” he begins. “One bookend is where you do very little virtual analysis, which is the build-and-test model. If the part passes, you move on. If not, you have to redesign and retest.
“The other bookend is using high-fidelity analysis models and spending lots of time in the virtual world before physical parts are made. In that context you are trading off real-world development time in favor of virtual-analysis time.
“My experience has led me to conclude that neither of those bookends are the way forward,” Jones states.
He believes that digital tools should be used to enable release of a prototype component as early as possible, with as few design variants as possible. The benefit of Hennessey being a low-volume player is that economy of scale is not a factor. It is more acceptable to produce prototype components and systems. “Any optimization can lead to big numbers in our world. We don’t have that economy of scale, so we can be more aggressive with our decisions.
“It’s a fine line. You must build the part expecting that it is fit for purpose. But the bottom line is, the sooner you have a running car, the sooner you’re learning, because you can’t always predict everything that’s going
to go wrong and go right. Sometimes the best thing you can do is to start testing and get that feedback,” concludes Jones.