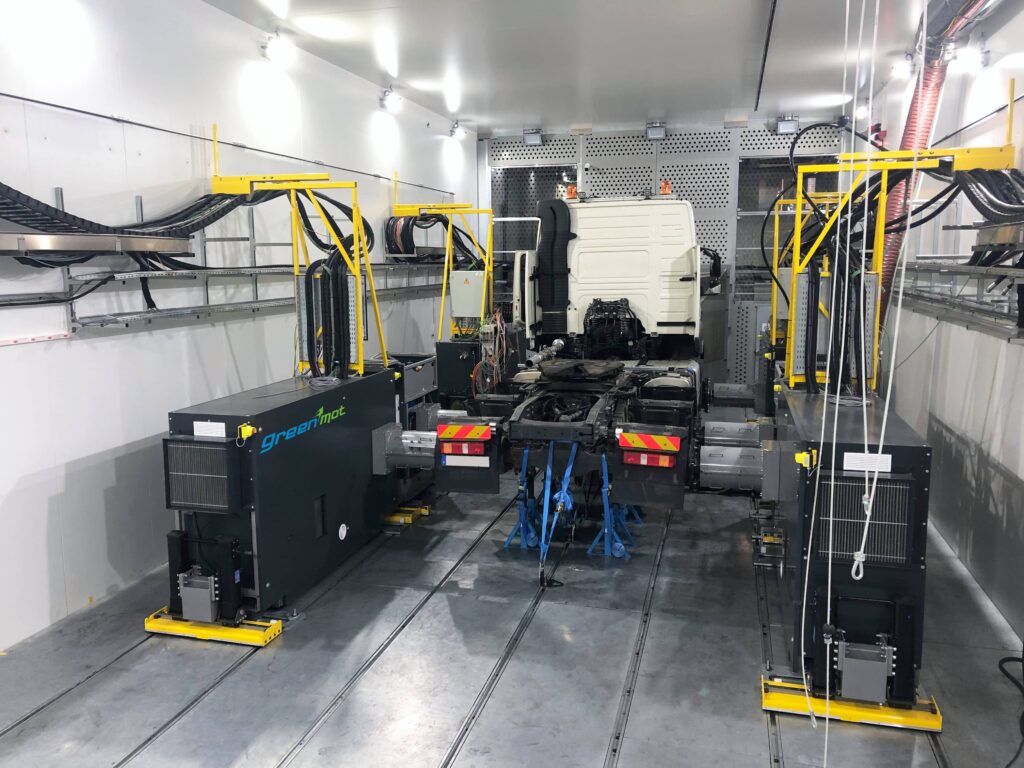
Two new heavy-duty vehicle climatic test chambers, housing bespoke test benches, green ventilation tech and robotic equipment, have been installed at GreenMot in France. ATTI gets the full details
After an 18-month development period and a €10m (US$11m) investment, French testing specialist GreenMot opened two new heavy-duty 1,056m3 (maximum volume) climatic testing cells in Villefranche-sur-Saône, near Lyon, at the end of 2021. The project represents a 10,000m2 extension to the company’s capabilities and has tripled its engineering resources. In total, GreenMot now has four test cells, including three heavy-duty facilities and a passenger car chamber. The expansion enables the company to respond to the growth in demand since 2020.
The specification for the new cells was based on customer requests. Stéphane Londos, president and founder of GreenMot, says, “We get a lot of feedback [from customers] on our facilities. It’s not a response to a very complex specification with hundreds of pages, it’s a system vision, which is designed to answer the real needs of the end user.”
Previously, with only one test cell for analyzing passenger cars and one for heavy vehicles, GreenMot had a six-month client waiting list. “The new cells enable us to take on customers with three-month campaigns (i.e. for durability tests) and customers with short-term campaigns (i.e. for a day) at the same time. The schedule is also much more flexible to cater to last-minute campaigns.”
Specified in-house by the company’s 40 engineers, one new cell can reproduce temperatures from -32°C to +63°C and the other can reproduce temperatures from -32°C to +55°C. Wind can also be replicated and solar simulation capabilities are available as well, up to 1,200W/m2 .
Each cell measures 8 x 22 x 6m (maximum internal dimensions), enabling coaches, industrial vehicles, construction vehicles, off-road equipment, military vehicles as well as articulated or double-decker buses of up to 20m to be examined.
Each chamber is outfitted with a high-power charging station, enabling clients to carry out endurance testing of electrified vehicles. The testing equipment is also designed to enable reverse engineering of buses or coaches before conversion to electric powertrain systems. This enables GreenMot’s specialists to gain a better overview of initial vehicle performance before transforming a vehicle.
GreenMot’s original two test cells (including one heavy-duty and passenger car cell) are outfitted with hub dynos, solar simulation capabilities, humidity simulation capabilities for replicating relative humidity of up to 90% as well as fuel and gas analysis technology. Inside the passenger car test cell, temperatures of -10°C to +45°C can be replicated; inside the heavy-duty test cell temperatures of -46°C to +55°C can be reproduced.
GreenMot’s inventory now includes two additional heavy-duty test cells. One is equipped with a hub-dyno and can simulate temperatures from -32°C to 55°C as well as humidity up to 90% and wind speeds of up to 110km/h. The other can reproduce temperatures of -32°C to 63°C, humidity up to 90% and solar exposure up to 1,200W/m².
Rinse and repeat
Repeatability and accuracy of results were a strong focus during the development of the two new chambers. GreenMot offers a driving robot, known internally as G-Robot, which can be configured to different driving styles for carrying out test cycles with the highest-possible repeatability. Special algorithms ensure a highly accurate speed profile, and provide flexibility and adaptability to test requests.
Londos notes, “Use of a driving robot eliminates variations of a human driver and means a test does not have to be time limited. Previously, the maximum test duration possible was around one or two [with a human driver]. Tests can now be performed for up to eight or more hours.”
Tests are managed through an in-house-developed human-machine interface (HMI).
In terms of equipment suppliers, GreenMot selected partners it knows well and that have a deep knowledge of the company’s technology. Siemens provided the electric motors. HBK supplied the measurement and data acquisition equipment.
Facilities operate Monday to Friday on a 10-hour shift. However, if needed, the test cells can run from 7:00am to 10:00pm in two shifts. Vehicles can be soaked overnight or on weekends, so a vehicle can be installed on a Friday and up to the specified temperature, ready for analysis on the Monday. Londos points out, “This is very interesting for foreign companies as the vehicle can be installed while a team travels, ready for the first operative day [of testing].”
The time it takes to set up instrumentation varies depending on the number of sensors needed, their type (standard or specific) and the lead times. “For a small instrumentation with 15 to 20 sensors, it can take one working day. For a large instrumentation with 300 to 400 sensors, it can take three to four weeks over a duration of three months. This includes the two-month delivery time for special sensors.”
Covid-19
Unfortunately, the pandemic affected client demand for GreenMot’s testing solutions. Like so many companies, this marked a difficult time for the firm. “The first cell was in operation in December 2020, but because of the sanitary situation, the grand opening took place in July 2021,” Londos says.
“The market has been really affected by Covid-19. Some borders remain closed, which is causing difficulties in us receiving vehicles and engineers.”
However, some manufacturers have been able to travel, and over the past 18 months GreenMot has carried out assignments for Irizar, Desautel, Iveco, Renault Trucks, Venturi as well as A2MAC1 and Cataldi for diversified tests. This has included analysis of electric and hybrid vehicles, diesel trucks, fire trucks, railway exchangers and a shuttle designed for use in the Antarctic.
There are plans to implement more test cells for smaller vehicles including cars and vans over the next couple of years. In the near term, according to Londos, the 2022 schedule includes some interesting test campaigns, which the company is looking forward to carrying out. This includes the retrofit of several heavy-duty vehicles, including buses and coaches, to battery-electric or hydrogen-fueled systems.
Full steam ahead
To minimize its carbon footprint, GreenMot carries out regular energy efficiency checks of its facilities, looking at all elements of its systems. It also assesses the complete energy flow of its test cells, as Londos explains: “We look at the potential energy losses to determine if we can save energy. We may even propose a new device that can save energy, to the customer. It’s about mindset rather than one simple technology.”
As an example, Londos examined the direct ventilation model for cold-weather simulation in climactic test cells. “I’ve seen cold simulation done through direct ventilation, which puts out air around -40°C, even in summer when the temperature outside was 35°C, but that makes no sense.”
In contrast, GreenMot’s cooling systems adopt a thermal recuperation approach. Rather than finding an extra source of energy, the company’s systems are designed to extract the cold air’s energy, thus increasing energy savings.