Having taken cues from land-based applications, synergy in the field of automotive Ethernet is providing a test case for scenarios that could influence other industries
Today’s vehicles aren’t just computers on wheels – they’re often an entire network. Onboard systems are collecting, receiving, processing and sharing ever-larger volumes of data, underpinned by faster and more complex Ethernet-based electrical architectures. It’s an evolution that’s changing how new models are designed and tested, too.
The foundations were set out with the BroadR-Reach specification over a decade ago. Developed by Broadcom, this enabled bidirectional data transfer at up to 100Mbps using a single pair of lightweight twisted cables – instead of two in each direction for a traditional Ethernet system. Backed by the OPEN (One-Pair Ether-Net) Alliance, of which Broadcom was a founding member, it formed the basis of the Institute of Electrical and Electronic Engineers (IEEE) 100Base-T1 standard, which has come to be used industry-wide.
As a sign of its importance, the OPEN Alliance now has more than 400 members, bringing OEMs, Tier 1s, silicon suppliers, Ethernet component manufacturers and test facilities together with industry bodies such as IEEE and ISO to develop new specifications. In turn, it’s evolved quickly – the IEEE is now setting automotive Ethernet standards for speeds in excess of 10Gbps, or 100 times faster than the earliest specifications.
Kishore Racherla, product line manager at Broadcom and a member of the wider Ethernet Alliance consortium’s board of directors, says these offer numerous benefits over other in-vehicle network (IVN) technologies, such as CAN, FlexRay and MOST.
“Ethernet is a flexible, switched, point-to-point networking technology, supporting scalability from low megabits to multigigabits per second. It eliminates the need for gateways to bridge from other technologies to Ethernet and enables reuse of robust existing local area network [LAN] protocols and security methodologies. It is also a lightweight solution, and is able to meet the stringent automotive EMC requirements,” he explains, noting that demands aren’t slowing down.
“Future in-vehicle networks will have to support higher bandwidths, hardware-based security and
time-synchronized networks [especially for aligning sensor data]. Automotive Ethernet will play a key role
in meeting these future requirements and, with its ability to provide end-to-end connectivity, will help
in reducing the number of IVN technologies used in vehicles in the future.”
Mixed signals
Automotive applications introduce some unique challenges. John Marrinan, director of application engineers, EMEA at Tektronix, says its tests assess systems for signal quality, impedance matching and error rates at the receiver, ensuring they conform to the IEEE 802.3XX interoperability standards. OEM approvals are especially stringent, often tending to require components to meet optional elements of the specification as an assurance of reliability, he says.
“Physical layer transceiver [PHY]-level testing is hard, with tight timing margins and many of the tests are pushing the boundaries of the instrumentation specifications. This has led to the industry developing solutions with greater levels of resolution and accuracy. The automotive Ethernet ecosystem was a contributing factor [in requiring those improvements] for these tests and others,” he says.
There are two ways to separate the data flow, Marrinan continues, each suited to different types of testing. Physically cutting the wiring system then using directional couplers to direct the signal toward the test equipment enables hardware-based fault triggering but at the expense of signal quality. Using software algorithms to analyze the current waveform is better for measuring quality, but doesn’t allow for real-time faults.
“Companies must think carefully about their test plan to access the signal correctly. Depending on the test requirements, in many cases multitest setups are needed,” he explains.
Kevin Kershner, digital solution system architect at Keysight Technologies, adds that in-vehicle systems need error correction mechanisms capable of coping with a much wider spectrum of interference than land-based Ethernet, and reliably transmit data for a much longer 10- to 15-year lifespan. In turn, compliance testing has to mimic a broad range of environmental effects to ensure compliance, especially as faster Ethernet technologies are more susceptible to noise.
“As data rates go up and baud rates go into the RF microwave range, there is a direct impact on receiver design and testing. With higher baud rates, there is increased electrical interference, plus noise sources, reflections, attenuations and other losses that impact signals. As the speed of signals increases, the wavelengths of those signals get shorter. Increased data rates require higher bandwidth receivers. This means the receiver is open to a broader spectrum of noise, including broadband environmental sources
as well as narrowband EMI attacks,” says Kershner.
“The signals are the frames from the [reversing] camera, the short-range radar for blind spot detection and long-range radar used for cruise control and lane keep assistance, so we cannot hope nor assume that things will work. The cost of the increased data rate, quantity, quality of frames in the camera and the number of sensors is [manifested in the] extra testing of the receiver before production.”
Cross-fertilization
Coupled with a move toward zonal electrical architectures, which network multiple ECUs, Ethernet is increasingly underpinning safety-critical processes. Illia Safiulin, product manager at Elektrobit, notes a trend toward network components – as well as end nodes – having to comply with the highest Automotive Safety Integrity Level (ASIL) D requirements, while also avoiding vulnerability from cyberattacks.
This is an area where automotive can learn from other industries. “One of the most important concepts to be learned [by the automotive industry] is cybersecurity. Currently it is one of the most important topics for in-vehicle Ethernet communication, and the experience from other fields is very important. Of course, there are certain peculiarities in the automotive industry that have to be kept in mind. Nevertheless, some firewalling or deep packet inspection techniques are of higher and higher importance,” he says.
“From the other side, the automotive industry can influence other applications from the standardization point of view. It was shown that having common standards/understanding of certain topics leads to more efficient development and compatibility.”
Ethernet-based electrical architectures are not only enabling richer infotainment and safety features, but also software-defined cars. It’s an opportunity to create new revenue streams and enable remote repairs and upgrades, leading to improved customer satisfaction, and automotive could spearhead innovations relevant to other industries.
Commenting on the opportunities for mutual learning, Amir Bar-Niv, VP of Marvell’s automotive business unit says, “The primary lesson is the importance of, and benefits associated with, the decoupling of hardware and software. With a zone-based electrical and electronic architecture, software lifecycles may proceed independent of hardware lifecycles; OEMs can regularly update software over the air. By moving to this ‘software-first’ architecture, auto makers gain the ability to monetize the vehicle over its lifetime and, importantly, to fix vehicle issues remotely just as computing and networking equipment is today.”
He continues, “Automobiles will be unique among ‘devices’ in their combination of autonomy, connectedness and software-defined character. This is likely to influence other systems and applications in ways not fully appreciated yet.”
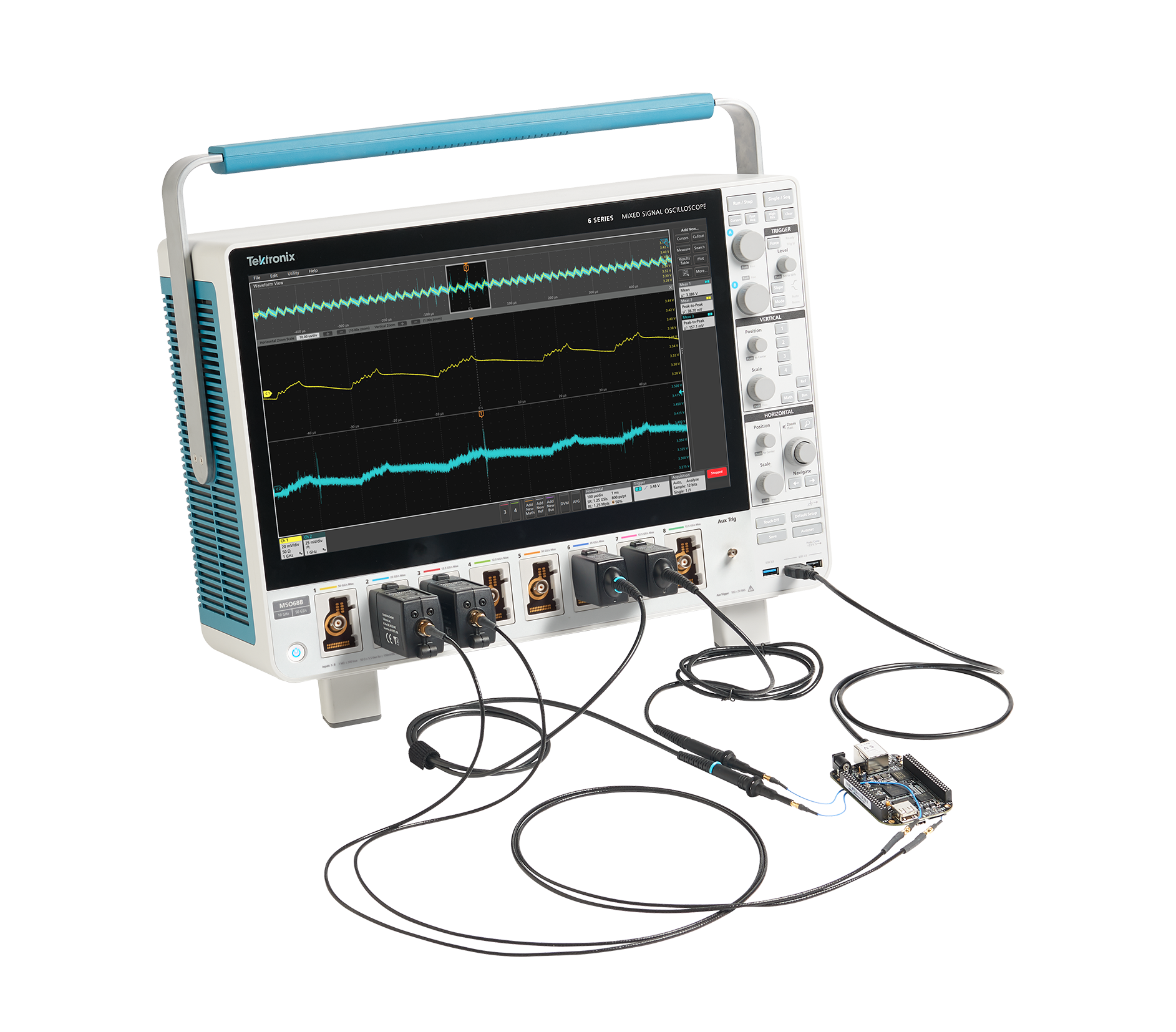
Inside information
General Motors began development of its new vehicle intelligence platform electrical architecture in 2017, as a foundation for wider electrification, safety and infotainment features but also for the Super Cruise assistance technology. Debuted in the 2020 Cadillac CT5, this can process 4.5TB of data per hour – five times more than its predecessor – and includes up to 10Gbps Ethernet connectivity. Most global models
will use it by 2023. Mike Colville, director of vehicle software architecture and core enablers at GM, says it also benefits vehicle development: “We have the bandwidth to configure/flash multiple ECUs at a time, some of which have very large software images that would not be viable over CAN,” he comments.
“Additionally, we have developed specialized tools for assisting with troubleshooting and verifying build
at the end of lines.” Development was supported by the company’s in-house product cybersecurity team, and the platform features protection from unauthorized access for both hardware and software. Early testing is carried out virtually, to identify problems before the hardware is designed. Colville continues, “Virtualization environments also lend us the flexibility of building predictable traffic models to assist us with developing the required TSN Ethernet configurations. This is an extension of the tools used in CAN system developments but with significantly increased data.”