How engineers at ZF Friedrichshafen built a new linear tester for a variety of applications employing Siemens drive system technology
The in-house mechanical engineering team at ZF Friedrichshafen in Schweinfurt, Germany, has developed high-end shaker technology based on an innovative linear motor concept. “The performance characteristics of our new acceleration test benches read like a who’s who of shaker technology,” comments Frank Stengel, head of the control engineering department at ZF Friedrichshafen.
Plant two, which focuses on special-purpose machine building and employs around 150 people, plays a key role in the company’s development of machine solutions. It designs and builds production and test facilities for a wide range of tasks, including for external customers.
Stengel comments, “On a global level, there are numerous applications for very dynamic acceleration test benches in the top-range power segment.”
The newly developed shaker is said to usher in a new era of test bench technology for very demanding tasks. “With frequencies of 50Hz and maximum accelerations of 40g (almost 400m/s²) for dynamic forces of 17.6kN, competitors don’t have much to offer here,” Stengel adds.
The new vibration test bench has a modular design and can easily be adapted to meet customer requirements. According to Thomas Heilmann, group manager for chassis projects at ZF in Schweinfurt, this means that “for even higher forces, several linear drives can be arranged in parallel and matched to each other by control technology”.
Iron-core servo drive solution with optimum control characteristics
At the heart of the acceleration test bench is a high-performance linear drive system, which enables performance requirements to be met precisely, and application-specific adaptation to a wide variety of test objects. The basis for this is the Sinamics S120 high-performance drive system from Siemens, and a linear motor based on Siemens’ Simotics L-1FN3.
Harald Skodowski, who is responsible for the test bench software at ZF, explains, “Due to the special design of the linear drive, we can achieve a high dynamic response and at the same time a good traversing quality. This has enabled us to optimize ‘cogging’ even with the extremely high force requirements.”
The term ‘cogging’ refers to the physical force ripple that occurs quite frequently in iron-core synchronous linear motors. This phenomenon was tackled in this application by a torque compensation feature in the Siemens drive system.
The key performance enabler behind the impressive dynamic characteristics of the new linear tester from ZF is the merging of the control engineering properties of coreless variants with the force yield of iron-core linear motors.
Intensive cooperation between the automation specialists at ZF machine building and the drive experts from Siemens mechatronic support in Munich enabled the team to achieve this, as ZF project manager Michael Friedrich confirms: “In an intensive customizing coordination process, we developed the lightweight secondary section design together with the Siemens experts, optimized it for the specific application, and then implemented the magnet assembly in a highly professional way.”
The result is said to be a highly dynamic drive with a significantly reduced dynamic mass, in which the leading forces are minimized by introducing a central force into the test object and by its design as a dual-chamber linear motor.
ZF’s Steffen Diroll, who was responsible for programming and commissioning the linear tester, says, “This means we can create complex motion profiles even with high test loads, and run through them precisely.” Even the forward and return strokes are controlled separately.
Customized servodrive as an energy-efficient overall solution
The Siemens linear servo drive, adapted for the application, is a development which, compared with hydraulic solutions, is energy-efficient and can be deployed more individually in terms of control technology than conventional mechanical crank drive systems. To compensate for the magnetic attraction forces and optimize the force density of the motor, a special secondary section equipped with magnets on both sides was developed, which moves between the permanently installed primary sections from Siemens.
Energy buffering with Siemens capacitor modules in the DC link of the Sinamics S120 drive system made it possible to reduce the feared ‘peaks’ in line-side power consumption. The ZF test benches with linear motor technology are therefore also suitable for mobile applications, as the ‘linear testers’ can be operated on the 400V three-phase network with 32A protection.
Even with high test object weights, this test setup is able to execute free motion profiles without any problems. Due to the compact dimensions of the linear drive and the high energy efficiency of the Sinamics S120 converter system, the test system could be designed very compactly, enabling mobile use with a 400V (32A) connection.
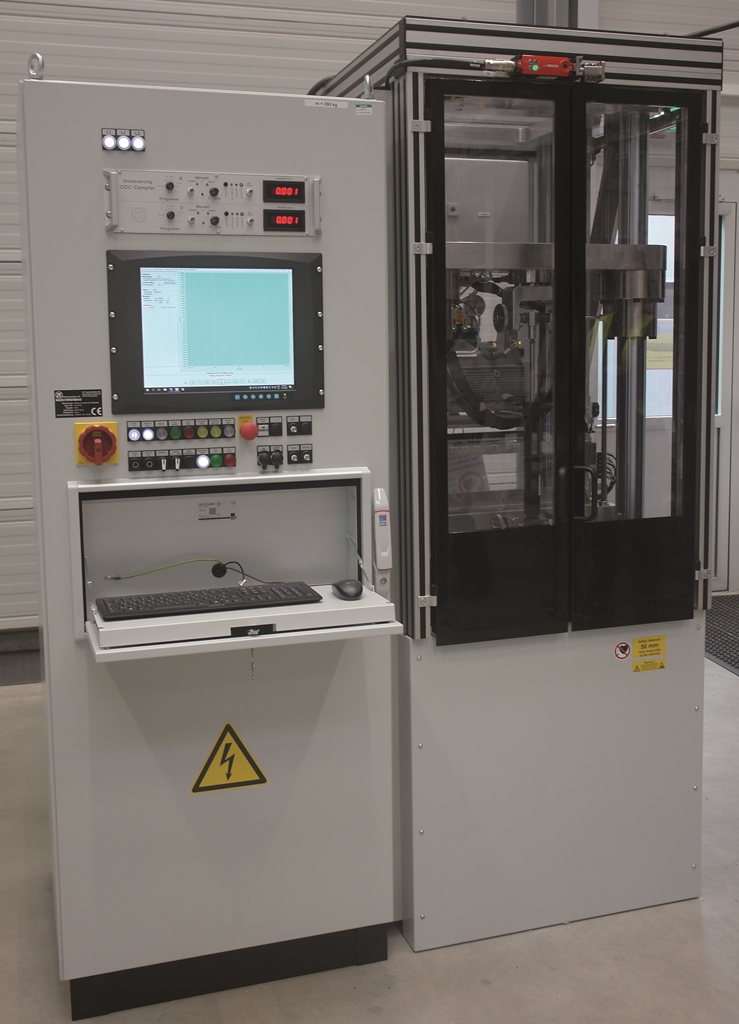
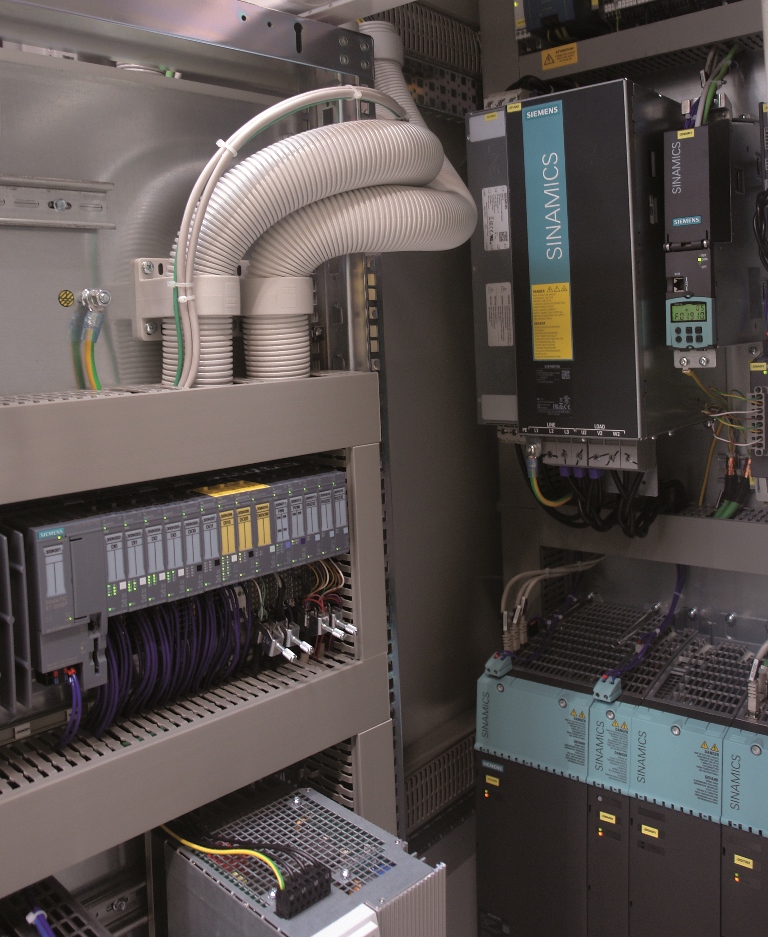