Researchers at the Politecnico di Milano in Italy are reaping the benefits of a cable-driven simulator to tackle the ever-increasing demands of vehicle development.
Tackling the wide range of scenarios that automotive developers face today – autonomous driving, active and passive safety, emissions reduction and electromobility – with real-world physical testing would be too complicated, costly and time-consuming, and can be dangerous.
Using a driving simulator is the perfect way to face these challenges and meet development targets in time. By setting up virtual test scenarios, engineers gain early insight into a system’s behavior, including the driver’s interaction with the car. Driving simulators already play an important role in the development of future vehicles, and more and more OEMs and suppliers are working closely together using this technology. The benefits for both sides are obvious: definition and confirmation of specifications, reduction of physical prototypes and real vehicle tests, no expensive travel to proving grounds, and more. Most driving simulators on the market use various kinds of traditional motion cueing methods, but these are very limited in their motion envelope and therefore guarantee only a partial level of dynamic perception.
VI-grade’s DiM400 driving simulator is a groundbreaking advancement in this field. It stands out from other simulators on the market by adding a unique cable-driven system to the lower stage, allowing for a greater motion envelope and longer time exposure to steady-state accelerations. This cable-driven simulator consists of a combination of two motion stages: at the bottom, an extra-quiet giant pulley moves frictionlessly and is pulled by polymer ropes wrapped around electrically driven winches; at the top, a new 6-DOF subsystem called a hexalift improves the motion envelope by increasing the available vertical travel with limited dependence on the other spatial motion simultaneously active. The two stages of motion are actively decoupled by a noise cancellation system. The first commercial installation of this type of driving simulator was recently completed in Italy at the Politecnico di Milano, which traditionally works closely with industry partners on the development of road vehicles.
Exploring innovations in vehicle systems
Located in Lombardy, Italy, which is a major region for automotive development with nearly 100 active automotive suppliers, Politecnico di Milano is a research institution collaborating with the best automotive companies in the world. The department of mechanical engineering is particularly involved in the development of road vehicle systems and deals extensively with areas such as NVH analysis, lightweight design and vehicle handling. The university conducts extensive laboratory tests on components such as tires, brakes and powertrains using finite element modeling, multi-body dynamics, artificial intelligence and big data analytics.
For this reason, Politecnico di Milano was on the lookout for the best-in-class driving simulator available on the market. Dr Giampiero Mastinu, a professor of ground vehicle engineering, contacted VI-grade in the course of conducting a merit-based and form-based process to identify the best driving simulator to fit the university’s requirements. Low latency and quick response times were fundamental requirements for the new installation – and are features offered by the VI-grade DiM400 driving simulator.
“The formal process, based on an international competition among all commercially available solutions, confirmed that the technology we were looking for was actually only available from VI-grade,” says Dr Mastinu. “Together with its harmonious combination of all sensory sources such as sound quality and vibration immersion, it helps to avoid motion sickness and provides a natural driving experience.”
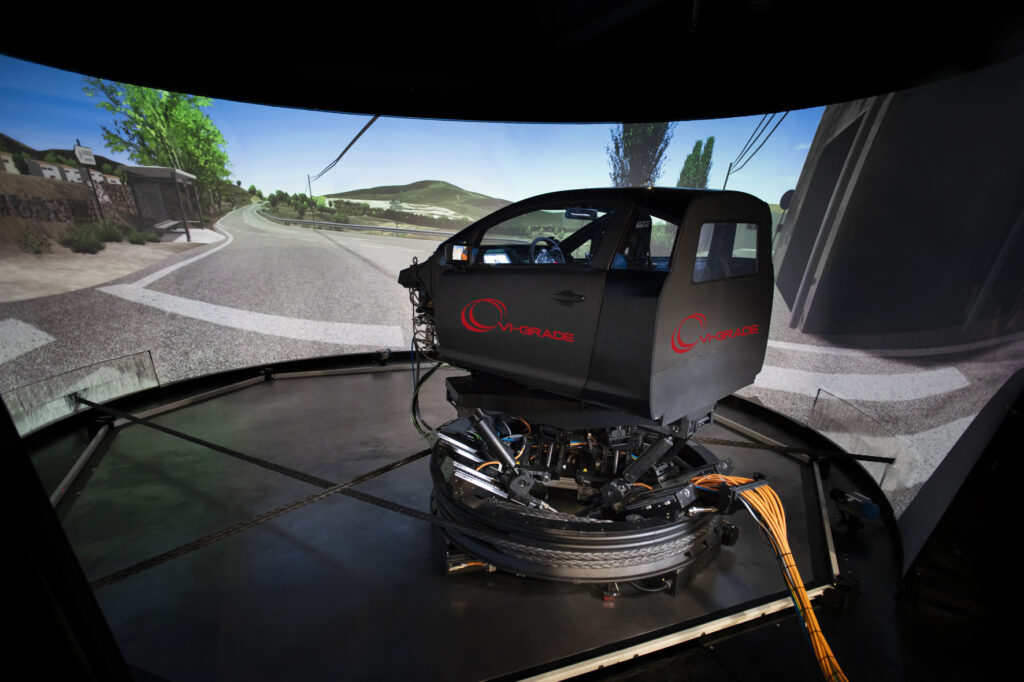
A cable-driven simulator for scalable, seamless adaptation
The idea for such a cable-driven simulator was conceived at the end of 2015, and a first patent application was submitted in 2016. “The objective was to go beyond the motion envelope limits of our current actuator-driven design,” recalls Diego Minen, CTO of VI-grade. “We wanted to create a new class of simulators that do not need any specific redesigns of their low-frequency stage in order to adapt to any footprint constraint or any specific target maneuver needs.”
To achieve this vision, the team adopted the simplest possible mechanical element able to control the three degrees of freedom of a frictionless sliding frame on a flat surface (called the base frame), which represents the instantaneous tangential plane on which every conventional four-wheeled vehicle is driving on. The air pads, which enable the motion platform to slide smoothly on the base frame, are housed inside the lower part of the motion platform (called the disc frame) around which the cables are wrapped. This solution enables three degrees of freedom (longitudinal, lateral and yaw) for the disc frame, giving it the ability to optimally exploit all the available workspace. In this way, the machine is kinematically and dynamically symmetric, which is vital when the simulation experiences large yaw angles. Positioned on top of the disc frame, the hexalift delivers an additional six degrees of freedom and is characterized by top-class heave displacement and high-frequency motions in all directions.
One of the special components of cable-driven simulators is the inertia compensation system. This system makes cable-driven simulators the first and only active simulators on the market, featuring a real separation of low and high frequencies. Through the motion of three calibrated masses, all vibrations coming from the upper part (the hexalift with its payload) are damped out and therefore not transferred to the lower stage (the disc frame).
A key advantage of this system is its scalability. Cable-driven simulators can easily adapt to client-specific budgetary and space requirements. They can be built in any size, ranging from 4m of surge and sway up to 15m and beyond. They are therefore configurable and scalable to any specific requirement for the type and degree of immersion. Dr Mastinu notes, “Thanks to the cable system, we are able to perform a passenger-car lane-change maneuver with almost no need to scale the physical accelerations. This means that one of the most important driving maneuvers for automated lane-keeping systems can be easily performed in our new driving simulator.”
New horizons for automated, green and safe vehicles
The new DiM400 driving simulator is situated on the university’s Milano Bovisa Campus for design and engineering degree programs, and measures 4.5 x 4.5m with a total footprint of about 13 x 15 x 6m including all accessories. It will be used for performance studies of vehicles and subsystems related to new material and component design using software-in-the-loop and hardware-in-the-loop simulations. These include discipline areas such as ride and handling, Real Driving Emissions applications, ADAS and the development of autonomous vehicles.
In addition to its technical advantages, the DiM400 is very easy to operate. After less than one month, the engineers at the university have been able to fully control the system by themselves for all kinds of maneuvers. This also helps with the second main focus of Politecnico di Milano: teaching and educating. With the new DiM400, innovative learning processes can be set up for the students, enabling them not only to model and explore innovations but also to directly experience their technical solutions in complete safety.
“The adoption of a driving simulator enables Politecnico di Milano to efficiently cooperate with automotive OEMs, which, thanks to the new technology, can demonstrate the competitive edge of their products, showing the positive impact on vehicle performance,” says Dr Mastinu. “We expect driving simulators to become more and more an integration platform for automotive development, as simulators open up new horizons for the automated, green and safe vehicle of the future, and deliver crucial insight early in the design process.”
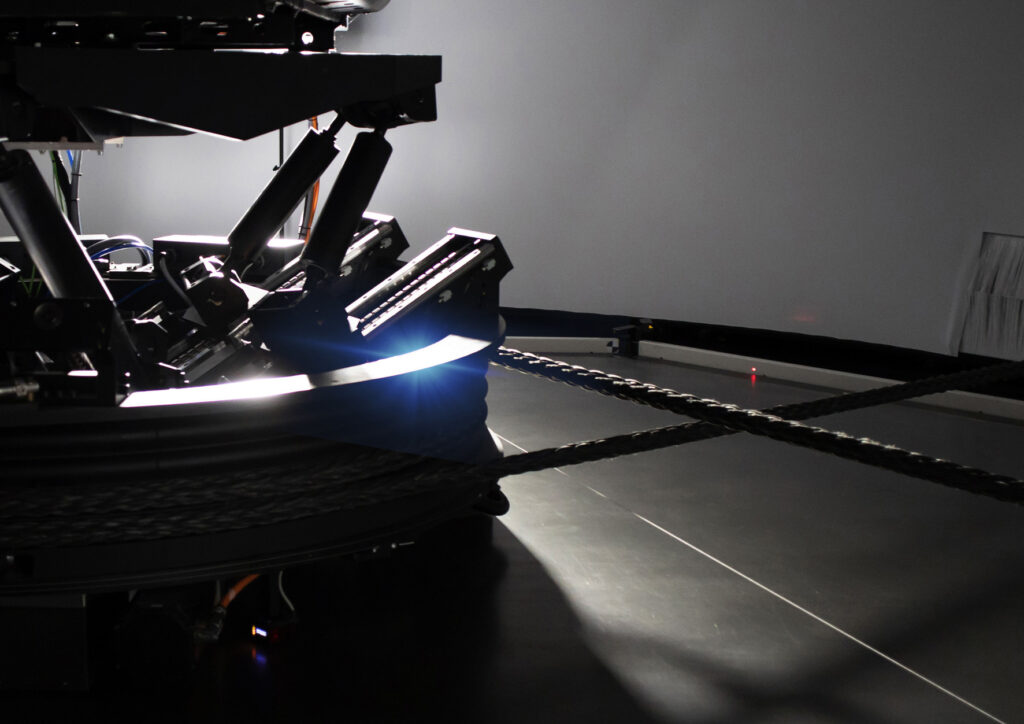