The challenge
The rapid evolution of electric vehicles has created new design, testing and measuring challenges for engineers. One of the most pressing needs has been in the area of vibration analysis. Engineers have struggled in particular to separate the harmonics coming from the slotting effect (i.e. air gap permeance fluctuations due to rotor and stator slots), and harmonics coming from the inverter.
Before 2011, asynchronous motor energy losses were assumed to be 0.5%. Ballpark numbers like that used to be considered ‘good enough’, but not anymore. Today they must be measured with far greater accuracy and precision. In fact, today’s asynchronous motors must meet at least the IE2 level of the IEC 60034 standard. Precise measurement of efficiency and energy loss requires the highest possible accuracy across the entire measurement chain.
Unfortunately, automotive test and design engineers faced a brick wall when attempting to make these measurements: how does one separate the frequencies caused by the inverter from those caused by the slotting effect? It was a real measuring challenge.
Two automotive R&D companies – Eomys and Dewesoft – with different expertise were presented with this challenge at the same time, and decided to work together to solve it.
The project
Figure 2 shows a typical test setup on an internal permanent magnet synchronous machine (IPMSM) with 12 stator slots and four pole pairs (12S8P). Eomys used a semi-anechoic chamber to measure motor and casing vibration noise up to 1,000rpm. The goal was to reduce the noise and vibration caused by harmonics induced by the inverter.
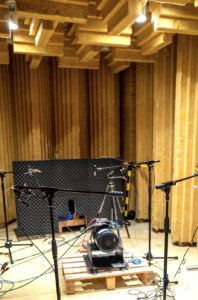
Figure 3 shows an FFT spectrum comparison of a noise and vibration spectrum at 863rpm, in this example. Measurements like these are useful, but they don’t describe the behavior of a system across its entire RPM operating range.
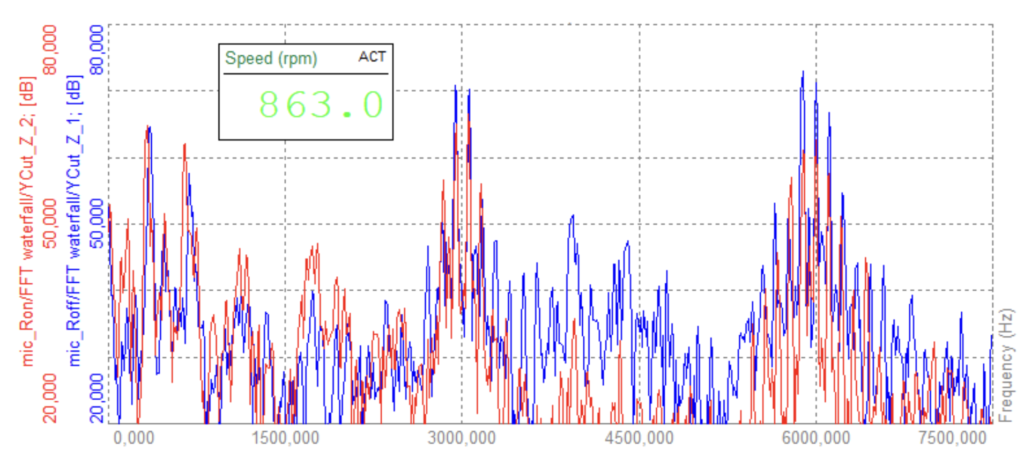
They also made spectrogram comparisons, as shown in Figure 4. These were also useful but provided only a qualitative comparison.
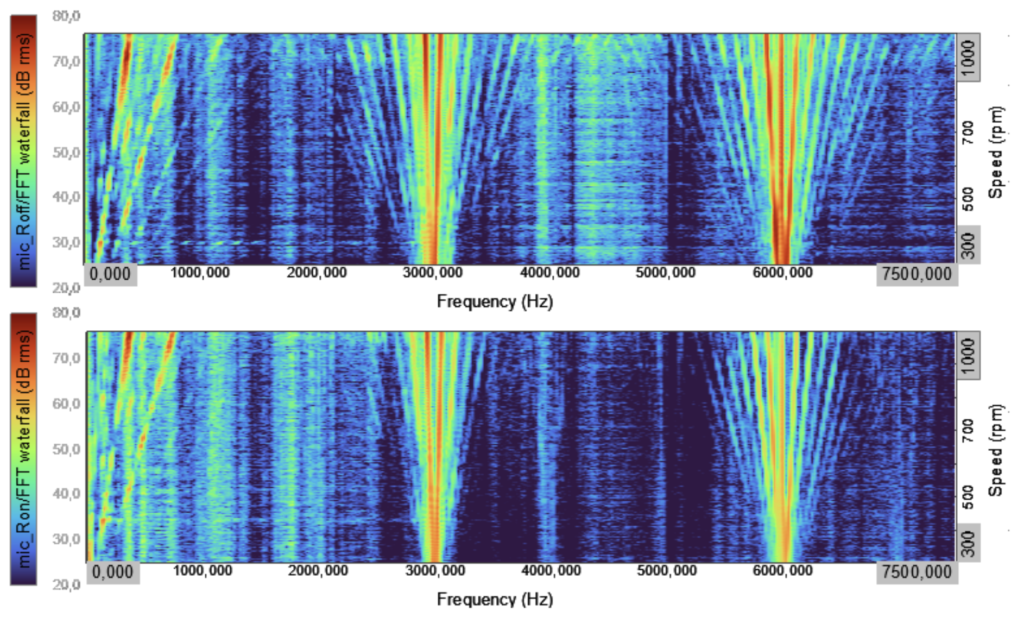
Using order analysis, it was possible to take the rotational speed variations into account by transforming the data samples per time (time domain) into samples per rotation (angle domain). FFT spectra based on angle domain data results in order FFT spectra where the spectral lines are related to the number of sinusoidal periods per rotation – regardless of motor RPM.
The solution
A suitable DAQ platform was required to perform the tests. Dewesoft’s Sirius DAQ instrument was selected because it can handle electric motors with up to 12 phases, and it can simultaneously measure mechanical parameters, such as speed, torque and deformation. The measurement of additional parameters, such as vibration, sound level, temperature, are precisely synchronized with the power parameters.
Normally these kinds of tests require several different instruments to be operated simultaneously. But the team found that a single Sirius system could measure everything, with all parameters synchronized. Additional parameters such as GPS position data, temperature, CAN bus data, and moving images from video cameras, could also be added and recorded in sync with the power data.
The input sensor channels were selected, and the tacho/frequency source was used to convert data from the time domain to the angle domain.
At this point, Eomys and Dewesoft engineers had a solution. Using this type of measurement and analysis setup, PWM flux and force harmonics could easily be extracted in an automated way during the measurement. It was also possible to add or adjust the mathematics afterwards, during post acquisition analysis, right inside the same software.
The bottom line
Using this technique, engineers can now easily split up and compare the influences of all such types of harmonic components and see how they relate to each other. They can monitor everything ‘live’ while running the test. This setup reduces testing time and provides both online and offline viewing of the results and all key parameters.
Vibration data can now also be used to validate the coherence between the PWM noise and PWM vibrations. In the same way, electric current data can now be used to validate the coherence of PWM vibrations to both the rotational speed harmonics and to the PWM flux harmonics of the electric current.
With Dewesoft measurement equipment Eomys was able to acquire and analyze all relevant physical quantities such as voltage, current, vibration and sound, and then perform advanced diagnostics for power quality and not only harmonics related to the engine rotation, but also flux and force harmonics related to the inverter PWM.
The motor manufacturer was pleased not only with the data, but with the fact that only a single DAQ platform needed to be used. The importance of correlating power measurements with electro motor vibration data is on the rise. New techniques and technologies to perform them in a more efficient and automated way are being developed to meet the demands of the electric vehicle market.