For development of its new hydrogen-powered race car, Forze Hydrogen Racing relies on Kistler technology
The Forze IX is the latest hydrogen-powered race car designed and developed by students from the Delft University of Technology. The zero-emissions vehicle features dual fuel cells. In the development process, multiple Kistler solutions were used to measure pressure, temperature, torque, and vehicle dynamics.
Founded back in 2007 when the hydrogen economy of the future was still a distant prospect, student team Forze Hydrogen Racing began by developing a small go-kart. Today’s Forze (Formula Zero) team is now working on the ninth generation of its hydrogen-powered vehicle: the Forze IX is a full-size Le Mans Prototype race car with excellent performance statistics – acceleration from 0 to 100km/h in under 3 seconds, a top speed of 300km/h, and fuel cell power of 240kW (600kW with boost). With their new vehicle, the Forze team competes against petrol-powered cars in the GT class of the Supercar Challenge, which runs from April to October each year – showing what is possible with race cars powered by hydrogen.
Formula Zero was a series of zero-emission motorsport championships held between 2008 and 2011, which the Dutch team won three times in a row in its early years before making the step toward full-size hydrogen race cars. It started every year with a new selection of students in August. About 30 full-timers and 30 part-timers now work for Forze, which eventually became an independent foundation, separate from the university.
Piezoresistive pressure sensors monitor fuel cell stack
Forze benefits from a diverse network of partners, including Kistler, which provides Forze with various sensors and systems for vehicle development: instrumentation to regulate the fuel cell stack is one key aspect, along with other more performance-related solutions. Development is still in progress on the new Forze IX, which will be the first in the series to have two fuel cells, thus doubling the power transmitted to four independent electric motors – one for each wheel. There are also four built-in hydrogen tanks with a total capacity of 8.4kg of the volatile gas.
In vehicle development, Forze uses a Kistler 4080BT pressure and temperature transducer – specially developed for racing applications – to measure the cooling fluid immediately upstream of the pump in the fuel cell cooling cycle. Since the temperature rise inside the pump is negligible, this transducer is also used to measure the temperature before the inlet of the radiator, which ultimately cools the cooling fluid.
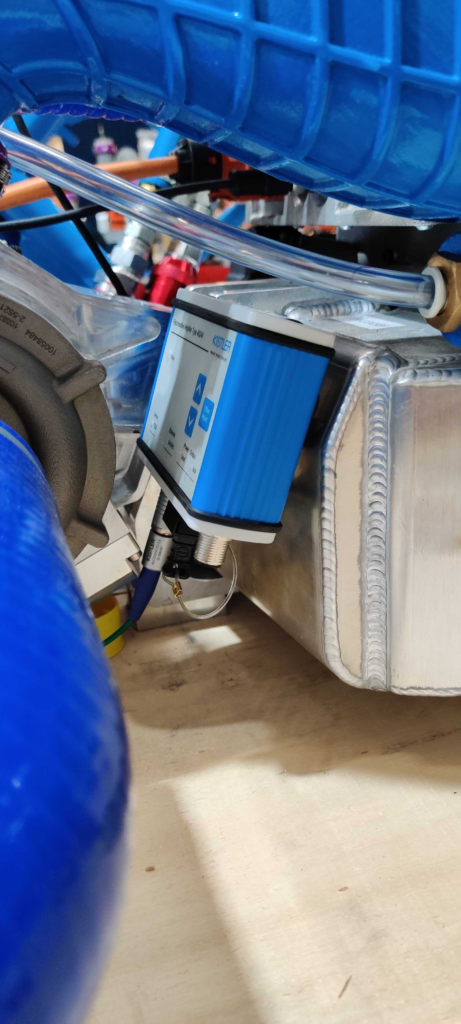
“This allows us to evaluate the cooling performance,” says India van Doornen, chief engineer at Forze. “We also use 4080BT transducers in the front and rear drivetrain cooling cycle. Especially here, packaging is a major challenge – so it’s very beneficial that the Kistler sensors are extremely small compared to the alternatives. And the sensors’ ability to measure both pressure and temperature makes them efficient to operate.”
A second piezoresistive pressure sensor, the 4007D from Kistler, is used on the cathode side of the fuel cell system to measure air pressure inside the fuel cell. “This is one of the most important sensors on the cathode side, because the compressor is such a crucial element,” van Doornen says. “It’s generally very easy to set up and customize sensors and amplifiers from Kistler for our purposes. So we didn’t need any technical support until now, but our contacts with Kistler have always met with fast and supportive responses.”
Head-to-head with petrol-powered cars
“Spreading knowledge about the technology, and promoting hydrogen and fuel cells are key elements of our work.” Forze will continue to apply even more Kistler technology in its vehicle development: one example is the Correvit SF-Motion racing sensor that can measure not only speed and lateral and longitudinal accelerations but also pitch and roll angles – highly dynamically and even under challenging environmental conditions.
“Thanks to its broad functionality and high accuracy, we can use it to evaluate large numbers of other sensors that are already integrated in the car,” van Doornen explains.
Last but not least, Kistler will provide Forze with a newly developed solution: the KiTorq DS sensor, designed specifically for high-performance automotive applications including motorsports. It will be used to monitor fatigue of the driveshaft, which is subjected to heavy loads when the accumulator boost is engaged. This new feature of the Forze IX is charged by recovering energy during braking and with excess power from the fuel cell; it achieves rapid acceleration, but also exerts a heavy load on the driveshaft compared to regular fuel cell power.
The team is planning track tests for the Forze IX, and its first race will likely be in summer 2024 during the next racing season.
The exchange between Kistler and Forze is a two-way process; Forze sends all of its data from the race track back to Kistler.
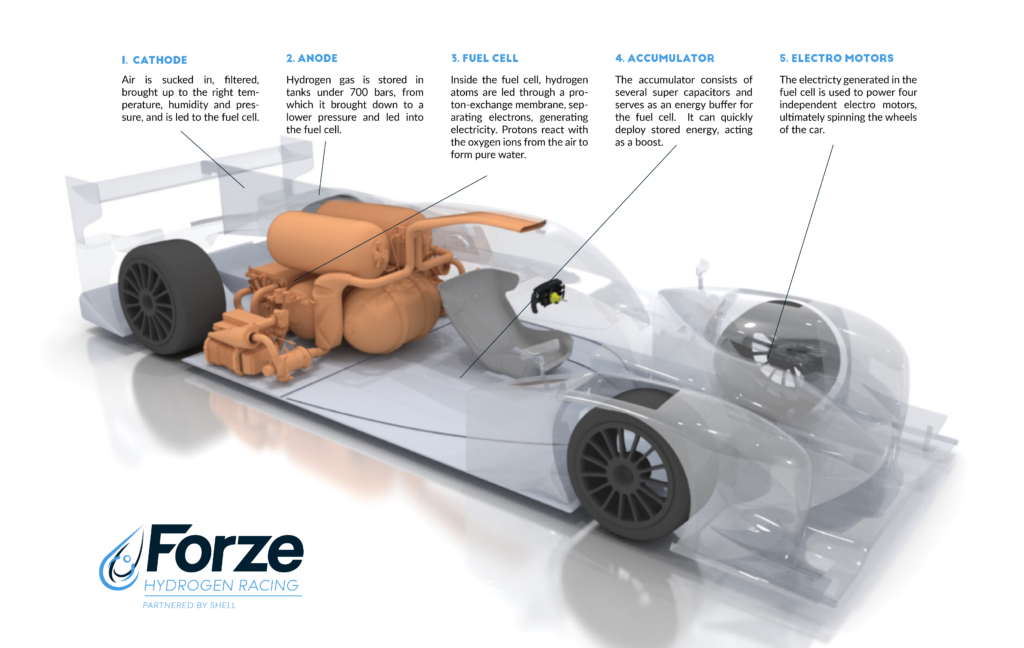