Evaluation of tire fitment options by direct measurement of the tire’s internal cavity noise, in 20 minutes per tire.
Road noise that penetrates a vehicle cabin contributes to driver fatigue and can be the factor that loses the sale or repeat business. All vehicle manufacturers therefore go to considerable lengths to reduce road noise.
Tire manufacturers play their part by optimizing their tire designs to reduce tread pattern excitation and achieve low transmission from tire to vehicle body structure. The road surface is, however, a continuously changing partner in the generation of vibration and hence noise. Without knowing the surface upon which the vehicle will drive, it is next to impossible to design for minimum transmission.
Many years ago, a senior engineer revealed that he had solved the problem of car road noise by fitting a louder radio to his car. For many years powertrain noise was the ‘louder radio’ effectively masking road noise. The advances in powertrain and effective mounting technologies have been gradually turning the volume of this ‘radio’ down to the point that road noise is the dominant component of cabin noise. Tire manufacturers, initially at the request of luxury vehicle brands, have been reducing tire noise at source.
If tread and carcass optimization proved insufficient to meet the vehicle manufacturer’s target, then a foam pad often around 90mm wide and 20mm thick is bonded to the tread liner (figure 1, below). This foam pad proved to be rather effective although it has brought, as always, some unwanted consequences.
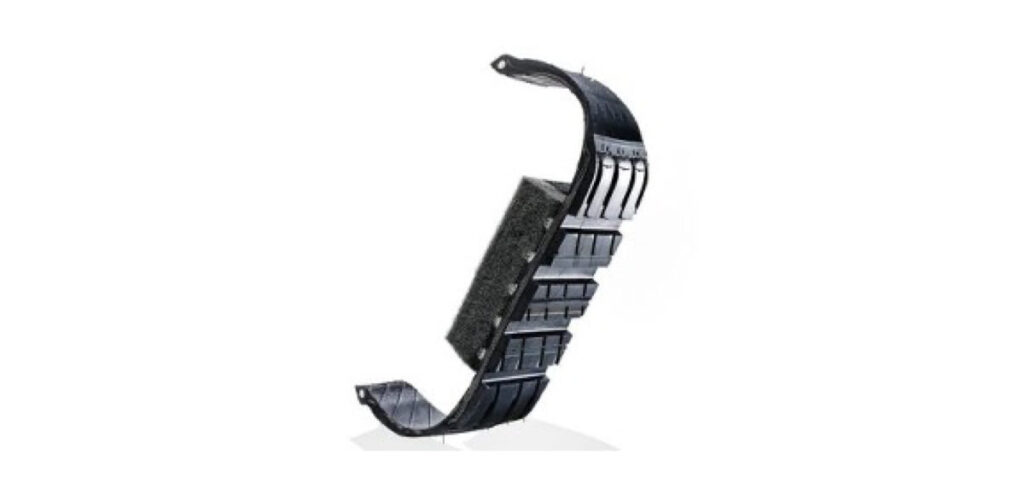
The foam adds weight to each tire and therefore increases inertia and energy consumption; i.e. it’s not a ‘green’ solution. If a tire deflates and is driven in this deflated state for 100m or so, the foam will be scuffed, and foam crumbs will be present in the tire cavity. These crumbs, if not removed during the repair, may get into the Schrader valve preventing it seating with consequent loss of air while driving. The puncture repair is complicated by the foam and may cause some tire fitters to refuse to attempt a repair.
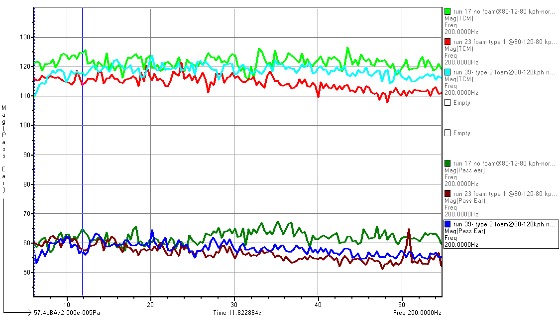
The good news, leaving to one side puncture repair, is that foam does absorb sound waves and its effectiveness can be assessed by comparing levels measured inside the tire and in the vehicle’s cabin (figure 2). Inside of the tire is important as this can be considered the source or input to the vehicle system.
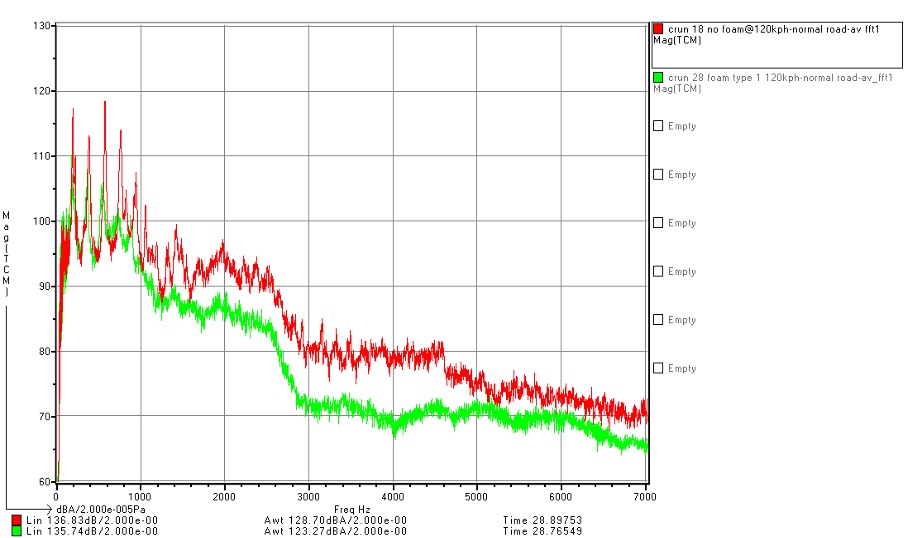
The measurements were made using the Bay Systems Tyre Cavity Microphone (TCM) system. The results show the A wt level of the third octave band that contains the primary cavity resonance. The first point to note is that all acoustic foams are not created equal; Type 1 (red) is significantly more effective in controlling the primary cavity tone than Type 2 (Blue). The data was taken using a luxury saloon car driven on a UK dual carriageway accelerating smoothly from 80km/h to 120km/h and back to 80km/h. The primary cavity tone was supressed by nearly 10dBA and the overall broad band road noise spectrum was reduced in level by 5dBA (figure 3). The two runs, with and without foam, were completed at a steady 120km/h.
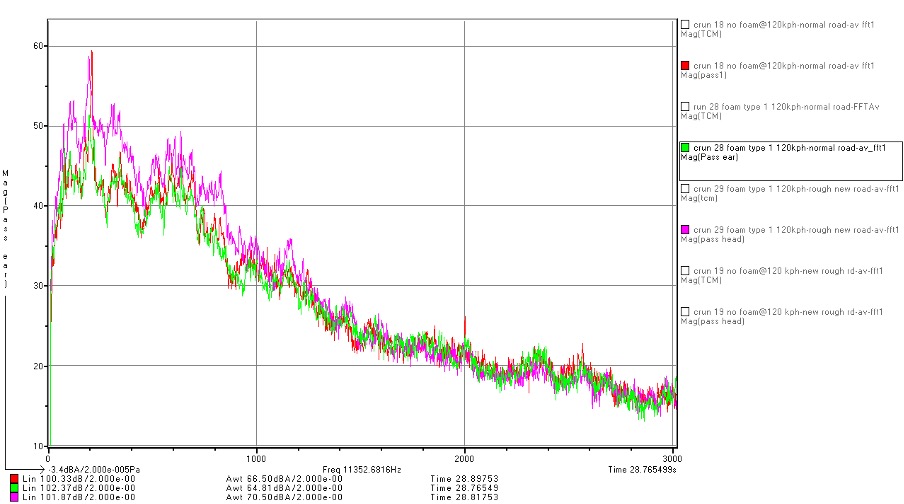
Inside the luxury saloon’s cabin, the benefit of the foam insert can be eliminated by a change in road surface. Figure 4 illustrates the luxury saloon cruising at 120km/h on polished asphalt and then a new asphalt; the red line is the cabin noise with no foam in the vehicles tires, the green line is with Type 1 acoustic foam and the magenta line is with acoustic foam on the new road surface. The primary cavity mode has returned to level before foam was added and rest of the spectrum is considerably higher in level. The A wt overall level has increased from 64.8dBA to 70.5dBA, a 6dBA step up in level will be noticed by all the occupants. The foam did not reduce the overall cabin level significantly, from 66.5dBA to 64.8dBA; i.e. less than 2dBA but the primary cavity mode dropped from 59.3dBA to 51.4dBA, an 8dBA reduction. Before the foam was added the primary cavity, tone was prominent, afterwards it was inaudible.
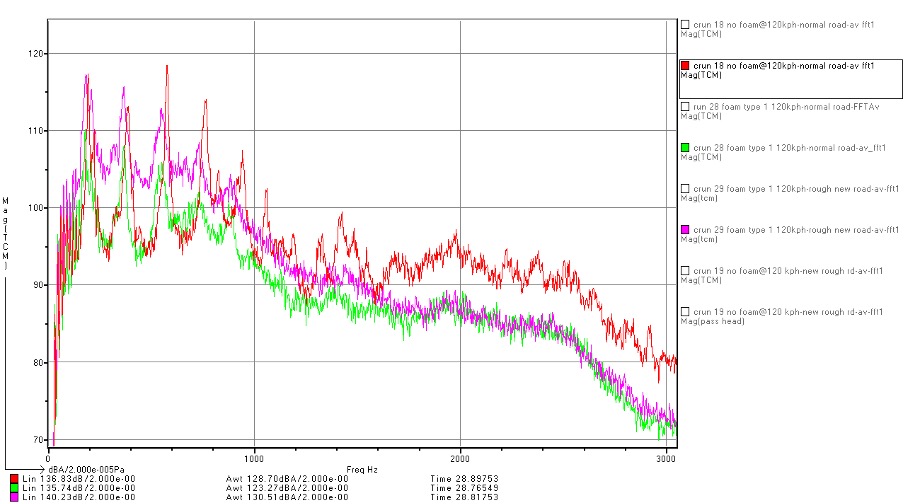
Noise levels inside the tire (figure 5) show a near perfect correlation with those in the cabin. The addition of foam reduced the primary cavity mode by 7dBA (117.3dBA to 110.2dBA). The new road surface increased the level to 117.2dBA. The overall noise level inside the tire was decreased by the addition of foam by 5.5dBA (128.7dBA to 123.3dBA). The change of road surface caused an increase of 7.2dBA (123.3dBA to 130.5dBA).
The effectiveness of any foam material can be measured using the standard tire test machine and a TCM. The absolute values measured will not be the same as would be measured on a genuine road surface but the direction of any change in performance will be captured.