*Sponsored content
World unique Kistler Hexapod receives ISO 17025 accreditation for multicomponent force and torque calibration.
Global standards such as ISO 9001 or IATF 16949 stipulate that automotive manufacturers and developers need to perform regular traceable calibrations on all test equipment used to measure quality-relevant characteristics such as wheel force transducers, multicomponent force sensors and dynamometers. For the calibration of those wheel force transducers and measuring wheels a complex multidirectional movable so-called hexapod system is necessary.
Its six-legged design enables calibrations with continuous load changes in six degrees of freedom: once the test object is mounted, movements can be carried out along three rotary axes and three linear axes, so that test engineers are able to measure torque and force in three different degrees without needing to re-position the object itself. Not only does this method provide more precise and reliable measurement results, it is also more time- and cost-efficient than conventional alternatives.
As of November 2023, measurement technology specialist Kistler adds another advantage to the mix: its proven hexapod for multicomponent force and torque calibration with continuous loading at its site in Sindelfingen, Germany, is now the first hexapod of its kind in the world to be accredited in accordance with ISO 17025.
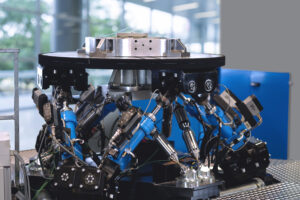
The hexapod from Kistler is able to apply force-free torque of up to 10kN.m and torque-free force of up to 50kN to test specimens, while at the same time also offering individual load ranges. The unique architecture enables the calibration of compressive and tensile loads through the zero point (push-pull) – but also compression (push) or tension (pull) only – and provides realistic and precise load modeling.
As a result, the calibration hexapod is ideal for the accredited calibration of wheel force transducers – with strain gauge as well as piezo technology – along with multicomponent sensors and dynamometers.
Cost-efficient and reliable results that take measurement uncertainties into account
The hexapod’s six-legged design allows test engineers to position test objects with high accuracy along three rotary axes and three linear axes and to measure and calibrate multiple forces and torques in a single test run. There is no need for test engineers to remove the test object and reposition it again. Multiple calibration points can be covered in one single configuration. Not only does the hexapod make the calibration process faster and more cost-efficient, but also less error-prone. The calibration results are in turn more reliable and precise. In addition, the calibration certificates provide a reliable statement about the measurement uncertainty of the calibration itself.
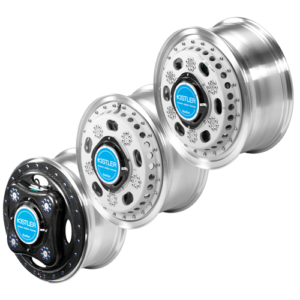
Expert calibration service for maximum quality control
It is essential for automotive manufacturers and developers to collaborate with calibration experts to ensure their test equipment used to measure quality-relevant characteristics is in compliance with international quality norms. Only after calibration can they answer questions like: Does our equipment meet its specifications? Which measurement uncertainty can be expected when using the equipment in my application?
By working with experts like Kistler, manufacturers have a reliable partner at their side that takes care of the entire calibration process for them: Once the test object is sent to the calibration laboratory in Sindelfingen, the experts perform the calibration itself and provide all the necessary documentation according to the international norm ISO 17025. This ensures compliance with international quality norms and standards like ISO 9001 and IATF 16949.
More on the way
Kistler’s recent accreditation in accordance with ISO 17025, by the German ILAC-accepted accreditation body DAkkS (Deutsche Akkreditierungsstelle), guarantees that the company will continue to meet and exceed the strictest industrial and research requirements in the future as well – and support automotive manufacturers and developers in complying with international norms for years to come. In fact, Kistler is currently working on achieving the same accreditation for another of its hexapods. The calibration system is able to simulate forces of up to 400kN as well as torques of up to 80kN.m – all to enable manufacturers to achieve precise calibration results in even higher force ranges.