Robust real-life testing has revealed fuel savings yielded by Jacobs Cylinder Deactivation (CDA) technology
Impending emissions legislation in North America (EPA 27) and Europe (Euro 7), covering both NOx and CO2 emissions, is pushing engine designers harder than ever before in the search for greater efficiencies. And separately, working from a 2019 baseline, the EU requires a vehicle-by-vehicle 45% reduction in CO2 by 2030, a 65% reduction by 2035 and a 90% reduction by 2040, using the theoretical VECTO measuring tool, which takes factors including aerodynamics and tire rolling resistance into account, alongside engine fuel consumption and exhaust output, in calculating CO2 emissions.
As seen at IAA 2024 in Germany, the market take-up of battery-electric trucks has not been as quick as had been hoped because infrastructure development is behind schedule. Focus has shifted to improving the performance of internal combustion engines and associated systems with manufacturers now looking for incremental reductions in fuel consumption across the entire vehicle from fuel injection to tire rolling resistance. This search will take them beyond their own R&D resources and into proprietary solutions offered by third-party suppliers.
Theoretical work and laboratory testing can only go so far in determining the efficacy of any proposed modification. Particularly where third-party suppliers are concerned, both truck manufacturers and their customers want verifiable proof that the product can deliver worthwhile improvements in a working environment. The problem is that real-life testing will inevitably include external variables that may exaggerate or conceal performance improvements. Weather and traffic density are two obvious factors, but other variables, including the human factor of driver behavior, are harder to define and more difficult to manage. The ‘signal’ of verifiable and repeatable change must be separated from the ‘noise’ of external factors.
This was the challenge facing Cummins Valvetrain Technologies (CVT) in verifying the on-road performance of its Jacobs Cylinder Deactivation (CDA) – a technology with the potential to reduce fuel consumption and CO2 emissions while also improving the efficiency of NOx SCR (selective catalytic reduction) control systems in low engine load conditions.
The theory behind CDA is simple. Most trucks are over-powered for the work in hand, most of the time. A 506hp tipper truck needs all that power when it pulls a full load up a quarry haul road but perhaps only half of that when returning empty to reload. Taking one, two or three cylinders out of six out of play has the potential to reduce fuel consumption in light-load conditions with little impact on productivity.
Jacobs’ system uses its hard-won expertise in valve control to automatically shut down selected cylinders in low engine load conditions by leaving their inlet and exhaust valves closed throughout the four-stroke cycle, while their fuel-injectors are also deactivated. This reduces fuel burn, and the parasitic pumping losses from needlessly filling and emptying the deactivated cylinders. When additional engine braking is required, the same components that deactivate the cylinders are re-purposed to provide vehicle retardation using the latest 1.5-stroke High Power Density version of the Jake Brake compression-release engine brake.
While the benefits of this are obvious on paper, quantifying them is rather more difficult. CVT chose the SAE J1321 standardized fuel consumption test with fully-loaded trucks on two routes: one highway and one distribution, on public roads in North America.
The tests were conducted using a 2018 International LT625 6×4 tractor unit with a 13-liter Navistar A26 450hp diesel engine and Eaton Endurant 12-speed overdrive AMT gearbox, both with a gross vehicle weight of 66,000 lb. Tests were run over 12,000 miles in Q4 2023 according to the SAE J1321 standard fuel economy protocol. The truck was run multiple times with and without CDA active, with the system engaged or disengaged via a dashboard switch. The truck recorded an average speed of 51mph on the highway route and 38mph on the distribution route.
Every run saw the test truck accompanied by a comparable control vehicle with its fuel consumption also recorded, to provide a baseline to account for variations caused by external factors such as weather and traffic conditions. Each route included trailer and driver swaps between the two trucks to eliminate those variables as far as possible.
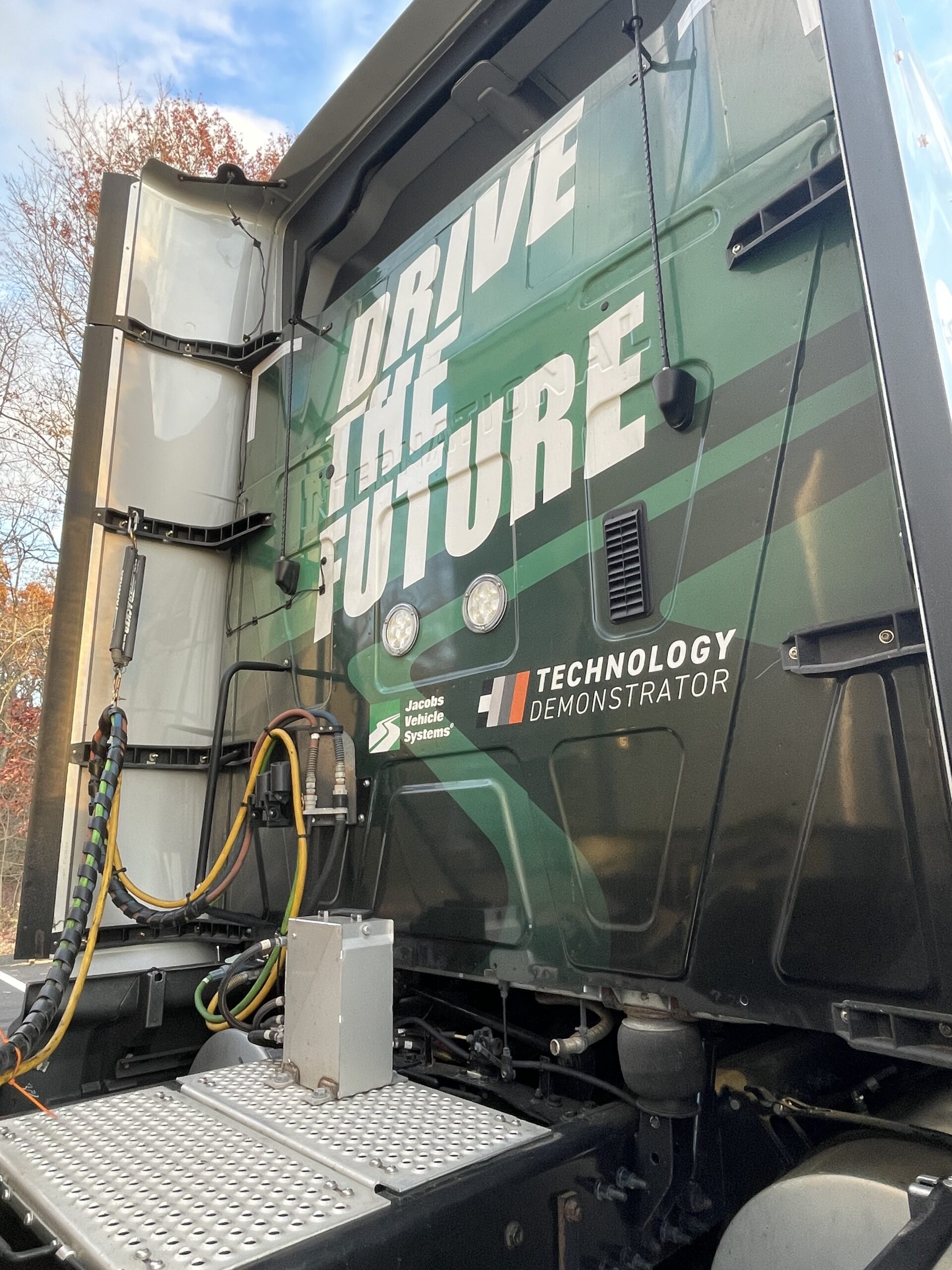
The on-road, real-world results from a fully-loaded truck followed initial fuel economy improvements of up to 20% in dynamometer-based lab testing of an engine in idle mode. In that same lab test, 77% reduction in NOx was recorded on a low load cycle with a 2018 aftertreatment system. While NOx emissions testing was not a focus for this latest road test, the test trucks had the same calibration compliance to EPA 2018 standards, and CVT expects these results to further improve for future emissions requirements where the benefits of CDA thermal management are further used.
Results from the road tests indicated fuel savings of 2.76% on the highway route and 2% on the distribution run; this figure may appear low in relation to the lab test, but CDA will always yield the greatest savings in idling, over-run and low-load conditions. The real advantages of CDA are likely to become more apparent in conditions where the payloads carried vary from run to run.
CDA saves fuel by reducing the number of active cylinders to match the drivers’ real-time torque demand. The active cylinders have higher loads and temperatures, while the inactive cylinders have reduced parasitic losses. The reduced air flow, and air fuel ratio in the remaining active cylinders, helps maintain exhaust system temperatures above the critical 250°C mark to allow efficient NOx conversion by the selective catalytic reduction module and continued passive regeneration of the exhaust particulate matter (PM) filter.
On the highway tests without CDA, temperatures in the truck’s SCR unit fell below 250°C for over 15% of the journey time, but when CDA was used in concert with the Jacobs Engine Brake, SCR temperatures fell below 250°C only during the scheduled stops and trailer swaps. On the distribution route, the mean temperature of the SCR unit was 243°C with CDA engaged, compared to 16°C lower without cylinder deactivation.
Time spent with the SCR operating under 250°C was reduced by over 21%, and SCR temperature with CDA only fell below 200°C for under 2% of the time compared to over 10% of the time without.
Jacobs’ CDA systems can now be found in over 30 development programs, with engines ranging from 2-liter to 16-liter capacity, and some programs have advanced into vehicle testing stage.
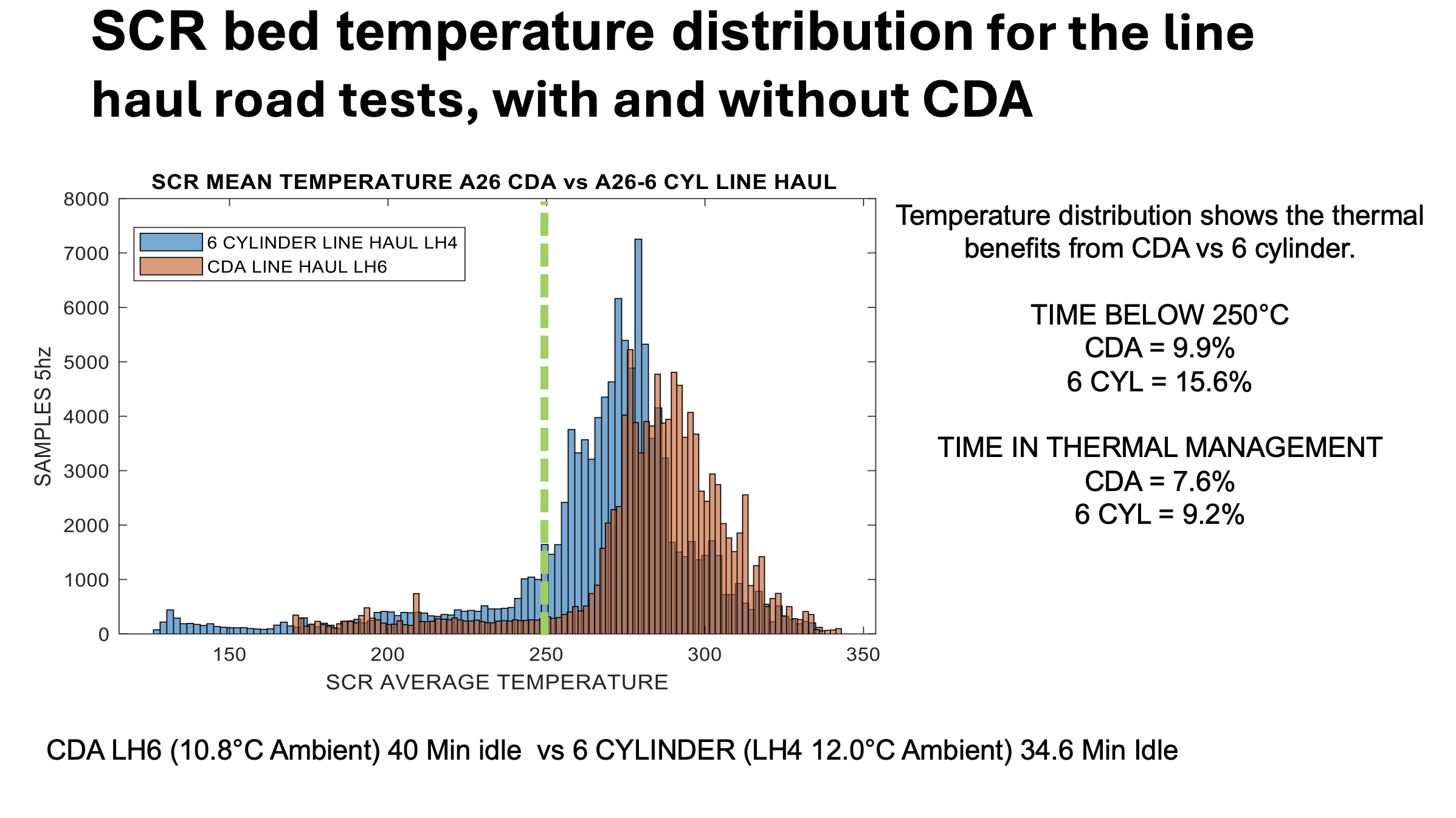