Florian Sailer, business development vehicle dynamics expert at imc Test & Measurement, details the measurement processes adopted on the Czinger 21C program for assessing vehicle dynamics and component durability
In every sense of the word, the Czinger 21C hypercar is built for speed. It is equipped with a 1,350hp hybrid powertrain, which combines a 2.88-liter V8 with an 800V electric motor and a regeneration system. When Divergent 3D – the manufacturer of the Czinger 21C – needed to test the operational stability of the vehicle, it planned a 14-day measurement campaign to optimize the car’s on-road performance. The tests were to take place on the Willow Springs test track 130km north of Los Angeles, California, where high-speed driving on bends and steep gradients was expected to result in dust ingress and vibrations.
The benefits of using a data acquisition system
There are different approaches to evaluating driving dynamics. Test drivers and racing drivers are often guided by their own perceptions and experience when analyzing and optimizing vehicles. Objective measurements for testing elements such as the safety of the chassis and other components, which rely on reproducible, technically verifiable measurements, differ from this. When testing the Czinger 21C’s handling stability and the durability of its components, Divergent 3D’s test engineers focused on technically verifiable measured data. By studying the forces and moments that act on the wheels from the outside, it was possible to verify and optimize processes and draw conclusions about, for example, different material mixes or tire profiles, and about the safety of the various assistance systems.
The requirements for the Czinger 21C test setup
A data acquisition system capable of accurately recording vehicle dynamics data and processing over 100 additional channels was essential. The vehicle’s top speed of 253mph [400km/h], the demanding test track conditions and the tight timeframe of the measurement campaign influenced the choice of data acquisition hardware and sensors. The measurement technology and sensors, particularly the wheel force transducers, needed to be sturdy enough to endure significant loads and be promptly available.
Divergent 3D used a test solution from imc Test & Measurement, a brand of Axiometrix Solutions specializing in automotive testing, which also conducted a workshop on the installation of the test solution. The test setup included the versatile and modular imc Cronosflex data acquisition system, four imc WFT-Cx wheel force transducers and other imc sensors, including the imc CLSx steering sensor. The latter recorded steering torque, angle, speed, acceleration and column vibrations in the x, y, and z directions. The complete test solution was designed to synchronously record and analyze the vehicle dynamics parameters along with accelerations, temperatures and pressures.
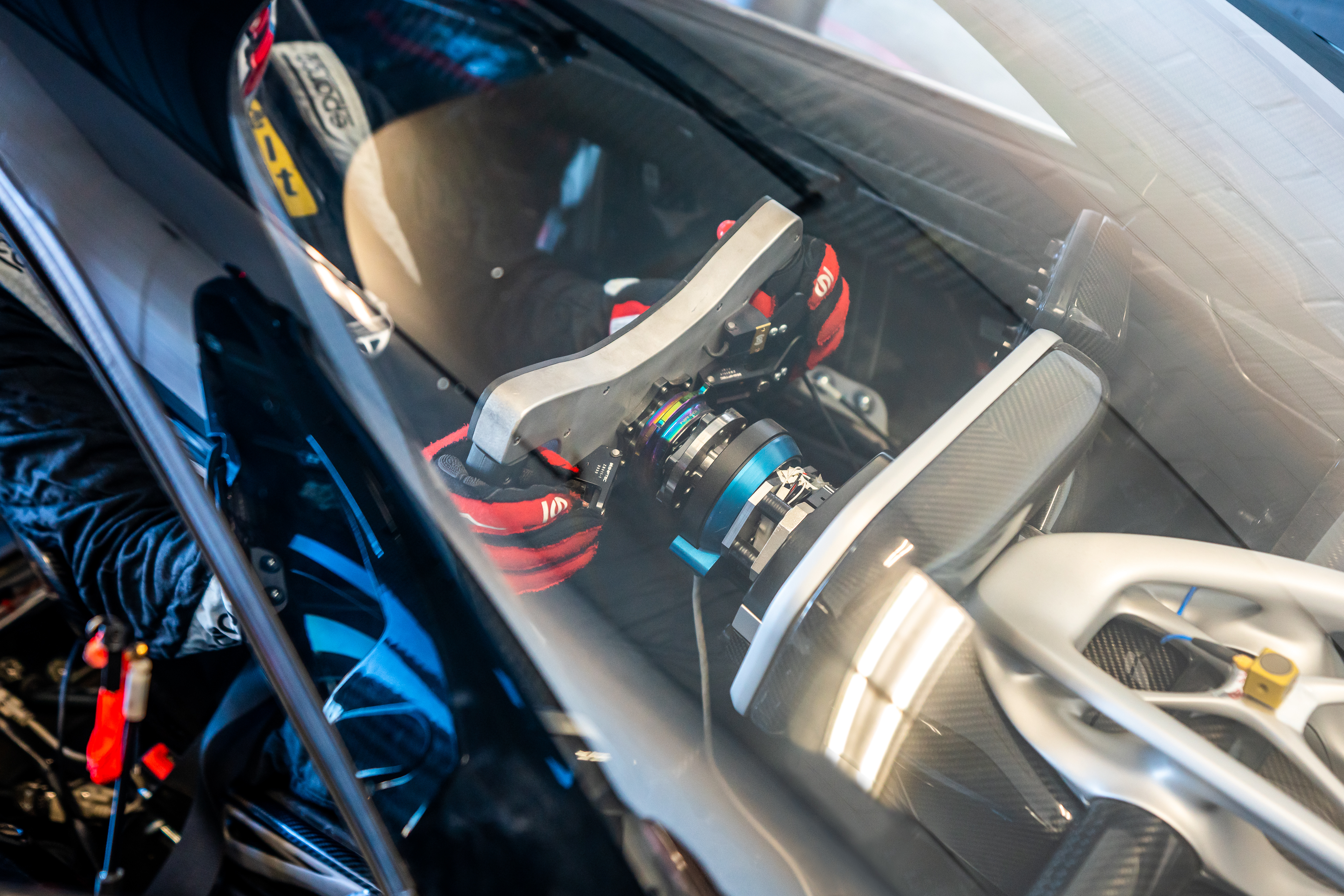
Which measurement data provides information about the vehicle’s response?
Today’s vehicles, such as the Czinger 21C, rely on electronic control units (ECUs) to function effectively. The Czinger Hypercar, for example, uses individual electric motors to drive each wheel, which requires safe operation even at top speeds of up to 235mph [400km/h] and while navigating dynamic corners.
Testing vehicle dynamics and collecting data that enables conclusions to be drawn about the synchronized cooperation between ECUs, including feedback from the vehicle, is crucial to optimizing vehicle performance. The wheels and tires play a central role in determining the stability and safety of the vehicle as they are the sole point of contact with the road. This is why a wheel force transducer was placed on each wheel. The drive and steering systems also significantly influence the vehicle’s driving dynamics. The driver’s steering behavior directly affects the wheels, which in turn affects the vehicle’s handling and stability. Real-time and precise insights into the interplay between the driver’s steering inputs and the vehicle’s reactions were obtained with the assistance of a steering sensor.
The analysis of the fatigue strength was also a crucial aspect of the improvement of the performance and durability of the vehicle. Some Czinger 21C components are made with the help of innovative composite manufacturing technologies, and the wheels, steering and drive axle are subjected to high stresses, especially during dynamic driving maneuvers. Therefore fatigue tests were conducted to gather data on various chassis components to assess material wear and component matching.
The measurement campaign enabled the engineers at Divergent 3D to expand their database and collect additional data on operational stability and vehicle dynamics. The testers gained a comprehensive understanding and insight that would optimize the continuous development of the car by shorter development timelines and improved properties of the 3D-printed components. Ultimately, this will contribute to a more refined product.
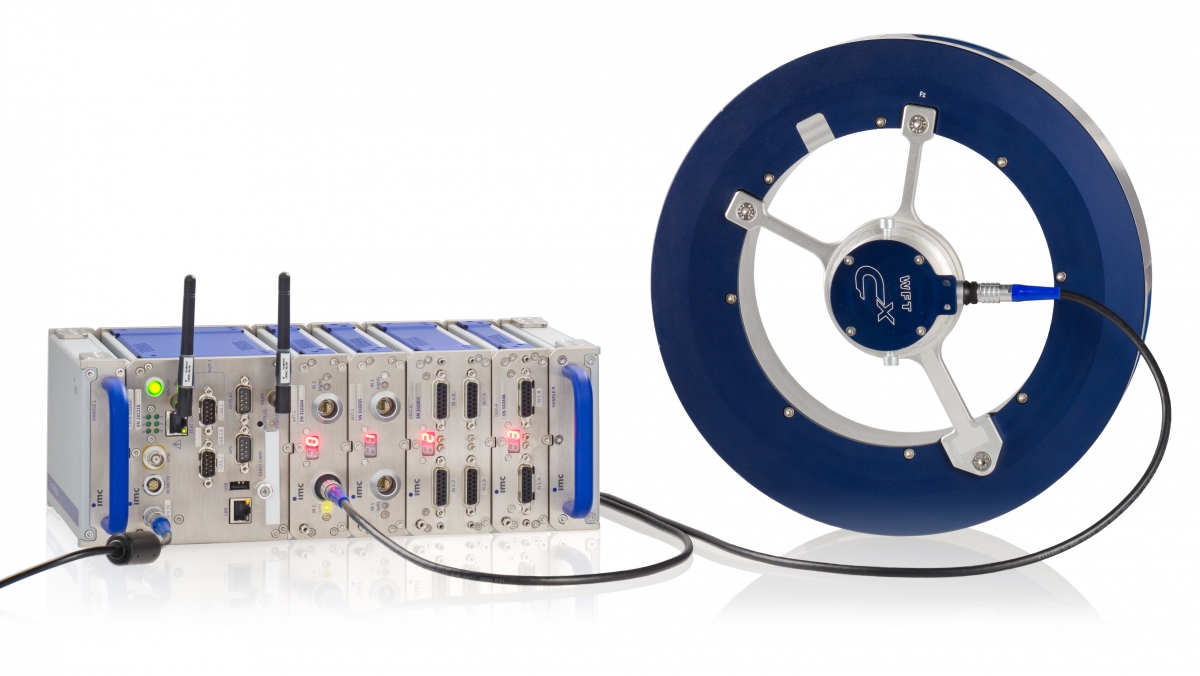
Why Divergent 3D chose the imc test solution
This project provided imc Test & Measurement with useful insights into new production and development procedures. Various factors influenced the engineers at Divergent 3D to advance the project with the imc data acquisition solution. imc’s fast project planning, on-site training, hardware delivery and user commissioning were the main deciding factors. In addition, the imc WFT-Cx wheel force transducer and the imc CLSx steering sensor impressed with their advanced technology. They include a simple and user-friendly installation, robustness and reliability, and complete integration into a comprehensive universal data acquisition system. Throughout the measurement campaign, the WFT sensor was used in both mobile tests and on the test bench, demonstrating its versatility and effectiveness.
Joeri te Hofstede, component and vehicle test manager at Divergent 3D, said of the WFT-Cx: “Accuracy, reliability, and handling are most important – and the WFT-Cx meets all criteria.”