*Sponsored article
CAE auralization – experience vehicles of tomorrow in the PreSense NVH simulator
Manufacturing physical prototypes costs time and money. Using NVH simulators like PreSense in the development process is an efficient and reliable alternative for manufacturers to evaluate part or component modifications without sacrificing human perception as a reference for the assessment. Auralizing the simulated drive noise makes CAE results more tangible in early development without needing prototype construction.
What is PreSense?
PreSense is an interactive, ultra-versatile, efficient software for simulating driving noise and vibrations. It allows drivers to experience and consciously trigger the sounds and, depending on the selected hardware, the vibrations of an actual vehicle in various operating states through resynthesized playback and excitation, providing a significant advantage over inflexible listening tests with prepared sound samples. Users can change the volume or modify and exchange noise sources – even the wind noise of a competitor vehicle, for example.
There are many different simulator systems that provide various immersion levels depending on the application and budget. They range from relatively low-key desktop simulators to the Head acoustics SoundSeat to full vehicle simulators, all fully supported by PreSense.
They all have in common that their acoustic models ground on measurement and/or CAE (computer-aided engineering) simulation data. This data is adapted in scope and type for the respective application and the required level of detail. Let’s look closely at the CAE auralization of an EV powertrain with the PreSense Mobile NVH simulator.
Case study: Experience EV powertrains in a mobile NVH simulator
The goal of the simulation is to predict if issues with tonal noise components would occur in a very early development stage since late changes are costly and time-consuming. At this early stage, the electric motor and its gearbox are only available as virtual models, not as physical prototypes. Nevertheless, the engineers would like to know if their targets for sound quality will be met. Evaluating the powertrain’s acoustic source properties is only part of the procedure. The most relevant question is how that motor and gearbox in a vehicle would sound together with road and wind noise – and could a minor issue become a severe problem, or will a noise component be completely masked? Getting clear answers as early as possible is crucial – and with PreSense, engineers and decision makers can do a test drive and experience the NVH performance.
The first step is to implement the powertrain into the vehicle virtually. CAE simulation tools calculate the source strengths. In this example, the transfer functions from the source to the driver’s ears have been measured at the predecessor vehicle, but it is also possible to use simulated transfer functions. The order levels vs RPM vs load with magnitude and phase and FRFs are loaded into PreSense to create a data set for the NVH simulator. Source excitation and FRFs are combined to calculate the path contributions and the overall sound. Road noise and wind noise data sets are taken from measurements on a test track.
The NVH simulator model can now be experienced in the Mobile simulator. The predecessor vehicle is equipped with a laptop running the PreSense Software and HXB PreSense, a calibrated headphone playback system with low latency and a built-in CAN (FD) interface. The engineers drive the predecessor vehicle but listen to the new powertrain via headphones. Now it is straightforward to validate which operating conditions lead to potential noise complaints and which are safe.
In addition, all signals of PreSense can be recorded during the drive. That includes the noise the driver hears and the operating states like speed, load and RPM. These files can be used for documentation purposes and post-processing. In this case, the hearing model tonality, a psychoacoustic analysis, shows whether a human perceives tonal noise components.
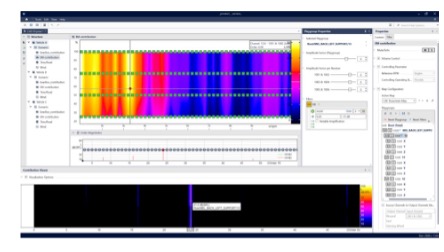
The online filter capabilities of PreSense can virtually modify the sound. Parametric order tracking filters make what-if scenarios audible and answer questions such as, Is it sufficient to reduce a whining noise by 6dB or 12 dB? With the help of PreSense, the engineers identify critical operating conditions, validate targets and investigate how sound can be improved. With this information, they can update the virtual CAE simulation model and assess the change’s impact.
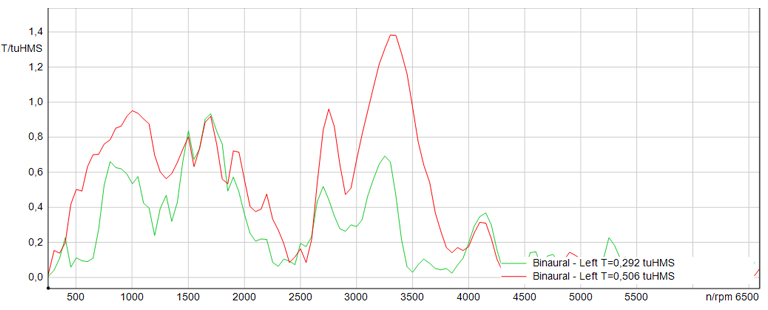
Summary
The PreSense NVH simulator is the ideal development tool to support users in the face of tighter cost and time targets and the resulting ongoing minimization of physical prototypes. Everyone can evaluate NVH performance instead of just analyzing diagrams and numerical values, which would require a high level of expertise.
CAE data auralization today enables early-stage noise quality assessment. The fast advances in CAE technology will lead to further improvements in NVH simulation – up to a virtual project sign-off.