Targeting S-Class levels of luxury and refinement from a blank-sheet all-electric platform, the EQS proved to be one of the most complex projects in Merc’s history – and it will leave an important legacy
The world’s oldest car maker is currently taking its biggest step yet into electrification. Although the EQS isn’t the first electric Mercedes-Benz, the luxury saloon is its first product designed from the ground up never to use a combustion engine, and it’s primed for ongoing changes. Half of the company’s global sales will be plug-ins within a decade, and all will be dust-to-dust carbon neutral within two.
Production of the EQS will take place alongside the new S-Class in Sindelfingen, but the two cars were developed separately and have almost nothing in common. The electric-only EVA platform incorporates a crash-proof battery compartment within a long wheelbase, and drive units either at the rear or at both axles.
The vehicle will be debuting at the top of the line-up, and for chief engineer Dr Oliver Röcker, the EQS had to live up to the S-Class legacy, without the advantage of generations of hindsight to work from.
“If a Mercedes-Benz carries the ‘S’ in its name, then it must be of the highest standard – it has to be perfect, so to speak,” he says. “The development methods are comparable, but with the EQS we started this from scratch – we couldn’t look at how the previous S-Class solved a problem, and how we could improve it. This was a very challenging project, and we have chosen very different solutions to the combustion S-Class because we have an electric-only platform,” explains Röcker.
These are familiar demands. Röcker joined the program around three-and-a-half years ago, having held similar roles within the development of previous versions of the S-Class and M-Class (now GLE) SUV. Demands on R&D are evolving at pace, he says.
“Development has changed a lot during the last few years. We are becoming more and more software driven within the car itself, but more and more hardware development is also being done by simulation. Today we simulate the whole car in crash testing, aerodynamics, even ride and handling, and in hardware we just do validation. Software knowledge is becoming increasingly important in our organization.”
Shape shifting
Recognizing that aerodynamic performance would be a vital component of its 700km-plus range target, the EQS’s cab-forward shape results from more than 1,000 calculation runs in a virtual wind tunnel, with fidelity high enough to require 700 CPUs.
Designers and engineers then made collaborative adjustments to clay models within the wind tunnels at Sindelfingen, tightening panel gaps, adjusting the shape of the mirrors and adding arrow-shaped wheel arch spoilers to optimize airflow for efficiency, cooling and downforce. With a flat floor and retracting door handles, the drag coefficient of 0.20Cd is said to make this the most aerodynamic car in the world, and sportier trim levels have little effect on that figure.
The lack of engine noise was a double-edged sword, removing some sounds but making others easier to hear. Flow simulations – validated by noise measurements using a microphone array and artificial human head, which can hear just like the real thing – informed the foam barrier between the battery and cabin, acoustic dividers in the tailgate and a unique trim between the A-pillar and windshield; cavities are filled with acoustic foam. Every moving part was chosen for its near-silent operation.
In tandem, engineers at the Mercedes-Benz Drive Systems Campus in Stuttgart-Untertürkheim were working toward similar goals, focused on powertrain NVH. Recent upgrades have introduced facilities for building and intensively testing electric powertrains, including 24 test benches that can supply direct
current to drive units, or installations where the full system, including charging systems, can be examined. These are adapted to work with the aggressive torque delivery of an electric vehicle during acceleration and regenerative braking – depending on the drive mode, the motor contributes more than half of the
car’s stopping force. Even the magnets and coils within the drive motors are optimized for minimal NVH.
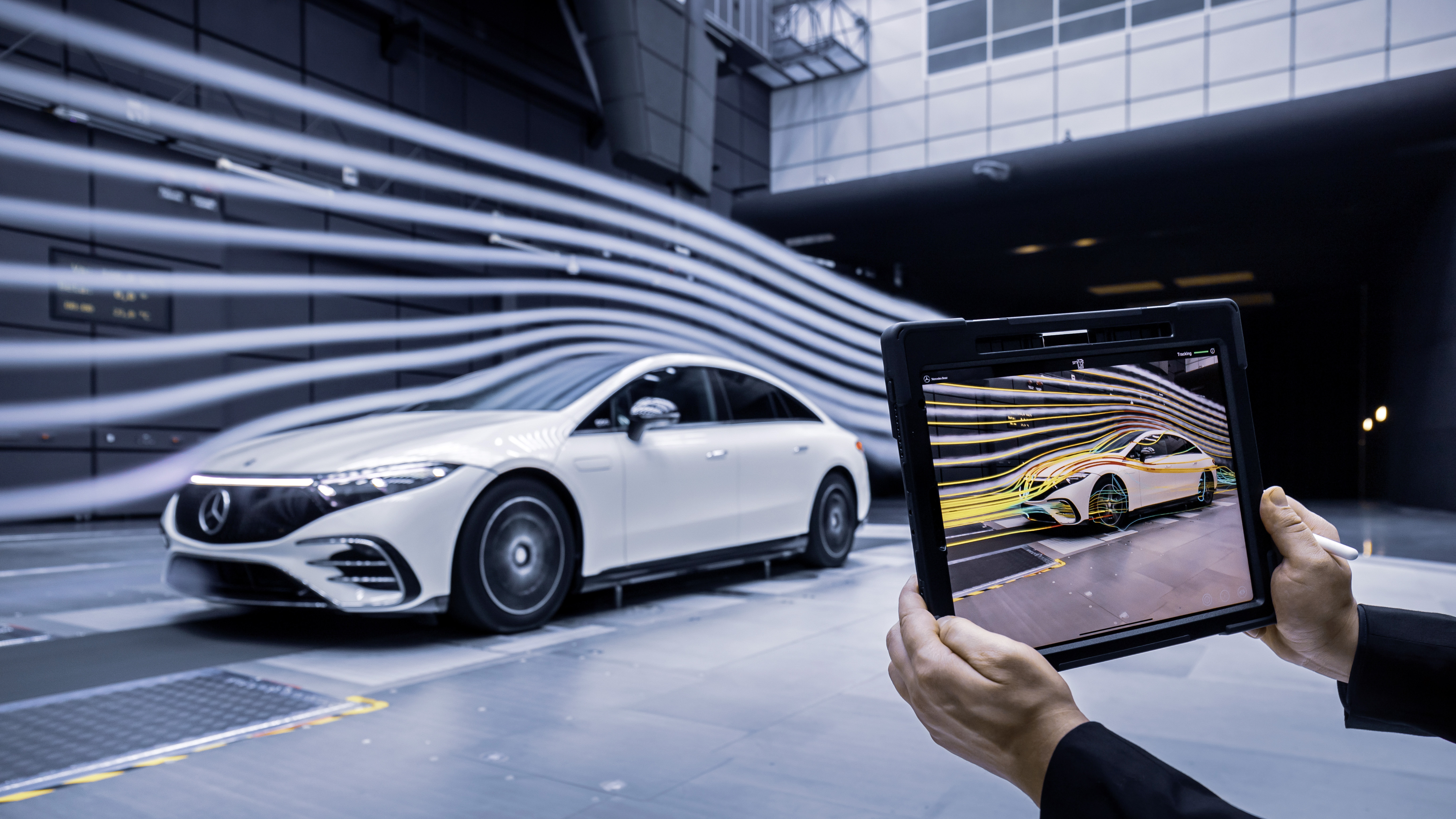
Energy levels
There were other important analyses specific to the platform, as Röcker explains: “In an electric vehicle, we don’t just test the driving [experience]. We tested the charging intensively in different locations, with different providers, in different climate conditions – rain, snow, very cold temperatures, charging a car that was cold and had been started just a few minutes ago – to find the best strategy to precondition the car, and so on. We have to check the interaction with the charging infrastructure, even in markets that don’t have the most extreme climate conditions, but have specialties in the power network.”
The EQS features up to 350 sensors that monitor the vehicle’s systems and its surroundings. Driver assistance and telematics features had to be validated with differing road layouts and signage. Prototypes were used to evaluate how the vehicles responded to heavy dust or snow, and to look for anomalies such as unwanted noises and reflections within the cabin that aren’t always possible to find in simulation. Engineers optimized how every kilowatt is used, regardless of climate.
“In an electric vehicle, every piece of energy counts,” continues Röcker. “If a system is not working, or it is not needed, then it should not take energy from the battery. We tested which systems were essential, how much energy they take and how to optimize that. It was intensive work.”
Of course, the payback is an abundance of useful hindsight for future vehicle projects. The platform is variable by wheelbase, track width and battery capacity – the EQS has up to 108kWh installed. The smaller EQE saloon and two SUVs planned for the platform will build on what’s been learned at the top of the range, and could influence the MMA compact car architecture, which is due in 2025. That said, despite taking steps into a new era, some familiar processes will remain.
“Simulation becomes even more important as the complexity rises,” says Röcker. “But at the moment, hardware testing has to take place to validate our simulations and make sure that a car that is carrying the ‘S’ in its name is ready for the customer. The combination of systems and the behaviors of materials, you can only see this in reality.”
Journey beyond
Efforts to centralize development proved timely. At Sindelfingen, the new crash laboratory includes facilities for testing electric vehicles, and battery packs were subjected to shock, penetration and overcharging tests in-house, as well as impacts to ensure safety performance exceeds regulatory requirements.
Facilities here are augmented by the company’s Test and Technology Center, an hour away in Immendingen, which includes road layouts, signage and traffic conditions simulating environments across the world. Mercedes-Benz aims to move 90% of endurance testing here – including cold-climate tests – and the EQS was an unexpected early case study.
“One of the major drivers [of the investment in Immendingen] was to reduce travel and reduce transportation of the cars,” explains chief engineer Dr Oliver Röcker. “It was very helpful to have all these facilities where we could intensively test the EQS, and we used them intensively during the project – also due to our traveling restrictions [because of Covid-19] over the last one-and-a-half years.”
Despite travel restrictions, progressively more mature prototypes have completed several million kilometers of on-road testing since the first chassis and powertrain mules were assembled three years ago. Röcker says most of the test locations are similar to those used for combustion engine projects. They included climate testing in Scandinavia across to the Middle East, high-speed driving at Nardò in Italy, and ride and handling validation spanning Asia and North America. Results from global teams were fed back to engineers at Stuttgart-Untertürkheim.
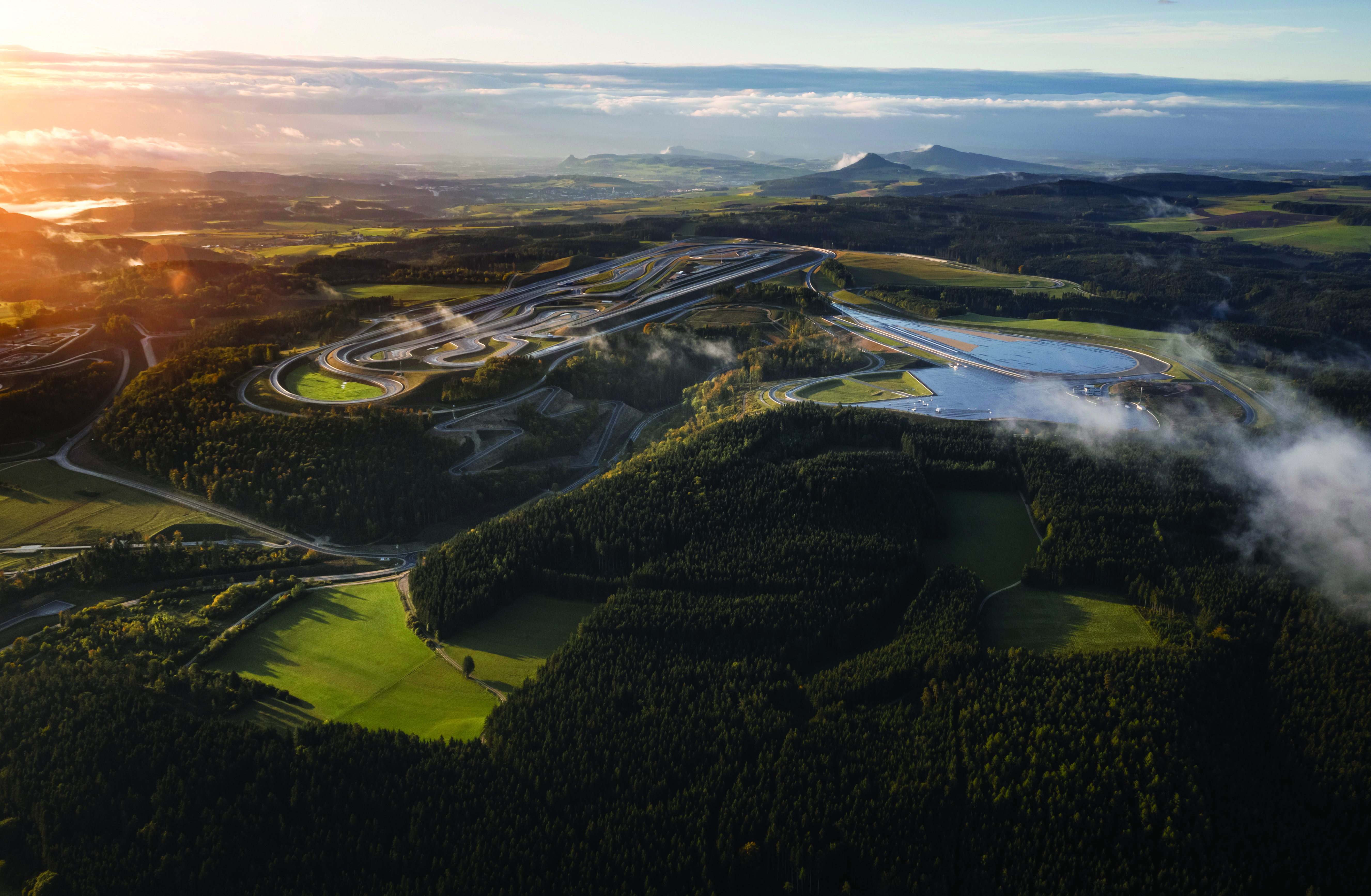