Six decades in the making, Daimler’s vast safety facility is adopting new technologies ready for diverse industry requirements, as head of the department, Rodolfo Schöneburg, explains
On September 10, 1959, the early demise of a W111-series fintail sedan would, in time, frame it as one of Mercedes-Benz’s most important vehicles. Its impact with a scrap metal barrier on a gravel track outside the Sindelfingen plant with a dummy on board marked the company’s first full-vehicle crash test, and the humble beginnings of what’s now a global program that’s still based on the same site 60 years later.
For just over one-third of that timeframe, this has come under the remit of the head of vehicle safety, durability and corrosion protection, Prof. Dr-Ing. Rodolfo Schöneburg. An aerospace engineer by qualification, he’s headed the department since 1999, overseeing the requirements of new markets and technologies, and shifting regulation. The backdrop is very different to 1959, but the ambition is similar: a holistic view of safety several steps ahead of legislators’ demands.
One vision
Today, Sindelfingen brings research and development, planning and production together on one site to improve the efficiency of new product launches, and crash testing is carried out within the vast Technology Centre for Vehicle Safety (TFS), which opened in 2016. Designed in consultation with engineers, the €3m (US$3.4m) facility is focused on better reproduction of crash scenarios, new technologies and closer examination of pre-accident conditions.
Schöneburg explains, “TFS opened up to the engineers numerous test facilities and completely new possibilities, for example for vehicle-to-vehicle tests, the configuration of assistance systems and Pre-Safe, and for the verification of vehicle concepts using alternative drive systems.”

Work here is fast-paced, comprising 900 crash and 1,700 sled tests each year, so the site is designed for high flexibility and time-efficiency. Its 8,100m2 crash hall has no internal pillars and uses a mobile partitioning system that enables four tracks of up to 200m in length to operate simultaneously. Engineers can access 70 configurations, including vehicle-to-vehicle impacts from any angle, and one of the five crash blocks can be rotated around its vertical axis to quickly change the barrier type, shortening preparation times.
Schöneburg says this has become a necessity: “Testing protocols and crash requirements are getting more intricate. More and more countries define their own requirements and even small adaptations lead to an extended outlay of crash tests,” he explains.
“Market requirements are increasing the broad Mercedes-Benz product portfolio, which has grown considerably, and due to the fact that we always go beyond the number and scope of the legally prescribed tests in our crash test program, the number of crash tests and crash configurations has steadily grown over the past few years.”
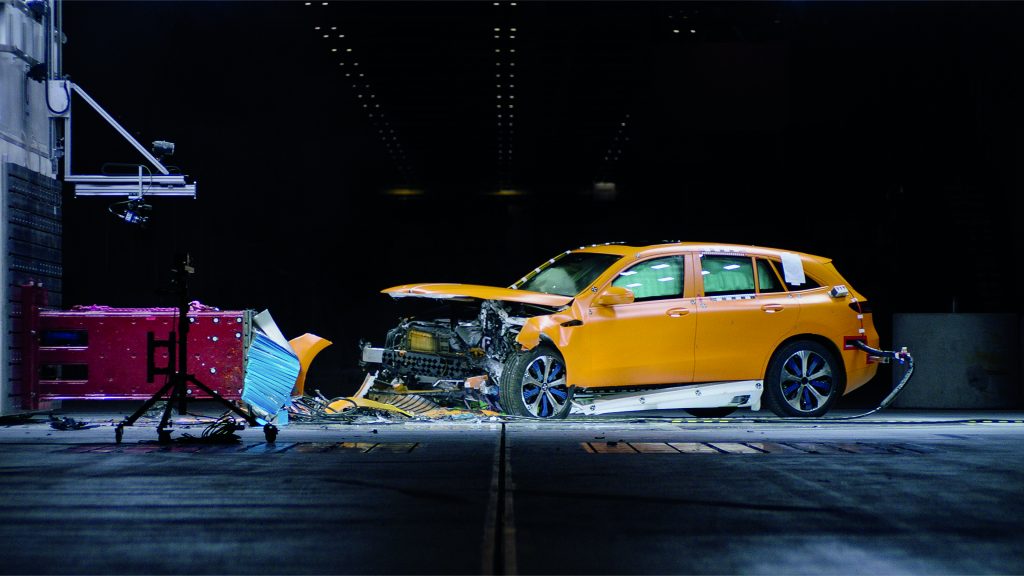
Around 40 of the impact configurations are designed around ratings systems, but TFS also offers facilities for Daimler’s own 50cm roof-drop test, plus stands for head impacts and an adjustable rollover ramp. New models are put through between 100 and 150 tests before production, with each recorded at 1,000 images per second by cameras alongside the impact and in 5m-deep filming pits. Sled tests are camera-tracked by a separate unit, minimizing the payload of the sled itself.
Under one roof
One of the biggest advantages Schöneburg sees for the TFS is its ability to incorporate a much wider variety of crash scenarios – including the company’s first indoor testing of safety systems for trucks. In turn, it offers ideal lighting and weather conditions, and the ability to document impacts on film, 24 hours a day, seven days a week.
Regulatory requirements are much lower for trucks than they are for cars. Trucks must be certified to ECE R29/3, retaining a survival cell following a 1.5 metric ton pendulum impact with the front and roof of the cab, and the A-pillars – simulating a frontal collision and rollover. Daimler trucks meet these requirements, but TFS will enable the company to develop additional testing based on accident data, to further improve passive safety.
Facilities are adapted to suit. The glass floor over the imaging pits is designed to withstand vehicles weighing more than 7.5 metric tons – five times more than a car – and the tracks are reconfigurable to suit different angles, impact speeds and barrier configurations.
“Trucks, vans, buses and cars are closely networked with each other and with our central research activities. It means that each business unit benefits from the developments and experience of the others,” says Schöneburg.
World service
New technologies are streamlining the process. Engineers are using augmented reality (AR) goggles to attach deformation measuring points during the preparation phase, and results obtained by photogrammetry are underpinning better correlation with virtual models. Scans are carried out on a turntable, with tools that will soon become fully automated, while unmanned drones follow yellow floor markings to ensure tracks are clear of personnel before a test.
“With colleagues in India and China, the accident researchers are also able to operate internationally,” continues Schöneburg. “The accident researchers in the Far East benefit from the expertise from Sindelfingen. With the help of AR goggles, they can compare notes with colleagues directly and in real time and thus conduct joint analyses even though the German accident research experts are not on-site.
“The user behavior and accidents in European and Asian countries differ greatly. The aim of the accident research in Asia is also to develop approaches for reducing the significantly higher number of victims compared with Europe, for example.”
Sindelfingen also offers better data collection. The site features a MicroTrack system that halves the width of the guide rails, from 180mm to 70mm, offering more complete image capture under the vehicle during a crash, and work is already underway to go a step further. Daimler is developing an interface to remotely control vehicles, which it says will further reduce configuration times, provide a greater degree of adjustment and better replicate the kinematics of a real crash by applying the brakes – something a draw cable can’t offer.
Schöneburg believes this physical element remains crucial, despite advances in digitization: “The current development program for a new, production-mature model comprises around 15,000 realistic crash test simulations with digital prototypes. Thanks to simulation, tests can now be conducted much more purposefully and efficiently,” he explains.
“Hardware testing will remain an important pillar of vehicle safety, and it’s important to also look at crashes on the roads, because not all accident constellations can be simulated in crash configurations, such as material properties, connection technology and kinematics – for example, chassis.”
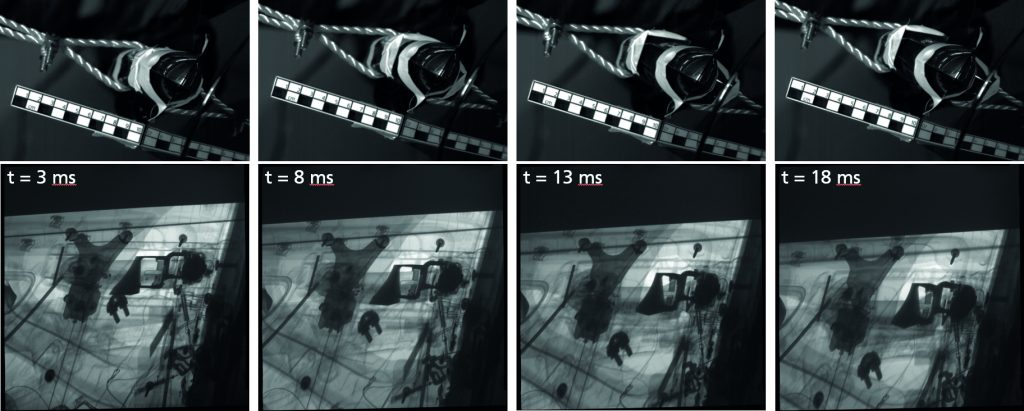
However, the two processes are closely linked. The company has begun collecting x-ray images of vehicles after testing, providing detailed examination of component performance and improving the accuracy of digital models. It’s also co-developing an active crash sled with TÜV Süd, which will enable low-volume, high-cost early body prototypes to be used for multiple early-stage tests of trim and door structures before full vehicles are available.
The only constant is change
Although it’s a long way from the gravel track and scrap metal that started the process 60 years ago, Schöneburg sees plenty of new challenges on the horizon as the company begins its seventh decade. “Besides the alternative drivetrains, we are facing challenges in new seating positions of occupants in automated vehicles. If the driver is not in charge of the driving task, he or she might take a more comfortable seating position, that in turn leads to new occupant protection concepts that need to be ensured,” he says.
“With TFS we not only cover the requirements of current legislation and rating standards, but are also equipped for the future.”